Injection molding is a highly effective manufacturing process by which plastic material is generally injected into a mold to form parts. This method is especially suitable for producing low-pressure gas valves to control the gas flow in heating systems such as gas appliances and industrial equipment. If it’s to be made reliably, safely, and in bulk, injection molding is the premier choice for making gas valves.
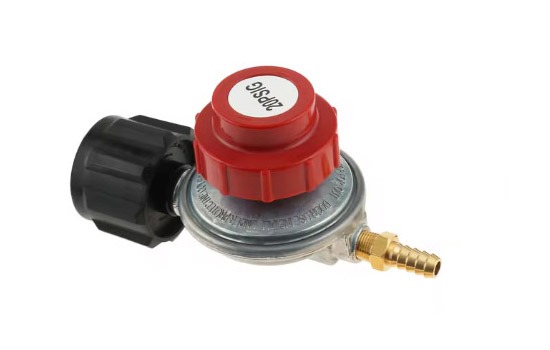
Injection Molding Process for Low-Pressure Gas Valves
Common Materials Used
Choosing materials for injection molding for low-pressure gas valves is essential to ensure durability and performance under operational conditions. Key materials include:
● Thermoplastics: They are often used because they are flexible and durable and also temperature and chemical resistant. Some of which you can sometimes find include polypropylene (PP), polyethylene (PE), and polyamide (PA) for strength and flexibility.
● Thermosets: Thermosets are materials that harden when heated and exhibit good strength and chemical resistance. They can’t be reshaped, and so are not used as frequently in gas valves as thermoplastics.
● Elastomers: These are rubbery materials, but with the properties of resilience and flexibility; they can act as seals for gas valves. Thermoplastic elastomers (TPE) are used when contention for elasticity and durability exist.
The Injection Molding Process
1. Clamping: First, the two mold halves are clamped together. Secure clamping is necessary to prevent material leakage during injection and ensure a consistent mold fit.
2. Injection: Molten plastic is injected into a mold cavity after it has been clamped. Control of injection speed and pressure ensures even filling of the mold and prevents air bubbles or voids, which are especially undesirable in gas valve components.
3. Cooling: After injecting, the material is allowed to cool. Cooling channels in the mold expedite this phase and help maintain dimensional accuracy. For gas valves, uniform cooling ensures the part’s performance integrity.
4. Ejection: Once the injected part solidifies, the mold opens, and ejector pins push the part out. This stage is critical, as any deformation during ejection could impact the valve’s precision.
Equipment and Machinery Used
Because low-pressure gas valves need precisely controlled machinery similar to that used in the injection molding process, injection molding equipment is specially designed for this job. The main components include:
● Injection Molding Machine: This machine has an injection unit to melt and inject the material and a clamping unit to hold and release the mold.
● Molds: The molds are precision-made. They are usually made of steel or durable metals that can withstand high pressures and regular use.
● Hopper: A funnel-shaped container holding and feeding plastic pellets into the machine to allow a continuous production process.
Advantages of Injection Molding for Low-Pressure Gas Valve Production
Using injection molding for low-pressure gas valves offers several distinct benefits:
● Complex Shapes and Designs: Injection molding supports intricate designs and fine details, which is crucial for gas valves, which often have features like thin walls, flow channels, and seal slots.
● High Production Efficiency: Cycle times are generally short, allowing rapid production. This level of efficiency is perfect for high-volume manufacturing—if the demand is there, it’s produced reliably.
● Consistent Quality and Dimensional Accuracy: Gas valves must perform safely and reliably, and they’re manufactured with stringent tolerance levels, so injection molding produces parts with consistent quality.
● Cost-Effectiveness: Once something is done and the mold is made, the cost of producing each part is very low, and the process is economical with large production volumes.
Material Selection
Selecting the suitable material is critical to ensure the valve can withstand exposure to gas, temperature fluctuations, and mechanical wear. Polyamide and polypropylene are famous for low-pressure gas valves, offering durability, chemical resistance, and consistent properties across temperature ranges. Material choice directly impacts valve life, resilience, and performance under low-pressure conditions.
Design Considerations for Low-Pressure Gas Valves
Certain design elements must be emphasized for optimal performance:
● Wall Thickness: Consistent wall thickness prevents warping or uneven cooling, which could compromise the valve’s reliability.
● Flow Paths: Properly designed flow paths allow for smooth gas flow with minimal turbulence, which is critical for valves where even minor flow irregularities could impact efficiency.
● Gate Locations: Placing gates in ideal locations ensures the mold fills evenly, reducing weak spots and enhancing the valve’s durability.
Process Parameters
Fine-tuning the following parameters helps achieve quality in gas valve production:
● Injection Pressure: Correct injection pressure ensures the mold fills evenly, which is critical to prevent defects.
● Mold Temperature: Keeping the mold at the ideal temperature promotes uniform cooling, preventing internal stresses that could lead to operational failure.
● Cooling Time: Allowing adequate cooling prevents shrinkage or deformation, which is essential for valves where precision is crucial.
Quality Control and Testing
Low-pressure gas valves are safety-critical components, so rigorous quality control is essential. Standard quality checks include:
● Dimensional Inspections: Ensuring each valve meets specified dimensions for a proper fit and function.
● Leak Testing: Testing valves under pressure confirms they can contain gas without leakage.
● Strength and Durability Testing: Ensures valves can withstand operational pressures and environmental conditions.
Real-world applications of Injection-Molded Low-Pressure Gas Valves
Injection molding has been successfully used to produce gas valves for various industries, including:
● Residential Heating Systems: Injection-molded valves regulate gas flow safely and efficiently in natural gas heating systems, balancing cost and reliability.
● Industrial Equipment: In industrial applications, durable injection-molded valves manage gas flow, ensuring precise operation in complex manufacturing environments.
● Gas Appliances: From gas stoves to water heaters, low-pressure gas valves produced via injection molding offer a safe, reliable option in household appliances.
Injection molding is an effective and cost-effective method for producing low-pressure gas valves that meet production rates with the precision needed for safety-critical components. Every valve is designed and rigorously quality controlled for material selection and meeting these demands, from residential heating to industrial equipment. By supporting complex shapes, dimensional accuracy, and large production volumes, injection molding remains an essential technique in manufacturing reliable gas valves that meet the stringent standards of modern applications. This robust method is indispensable for manufacturers seeking a reliable production technique for these crucial components.