The production industry is a wide one. Companies make products from many materials. Many products require certain materials. Companies use many production processes to ensure that they create the right item to ensure the satisfaction of their customers. Processes may be different, materials may be different, but the end result is that quality product.
However, there are some popular processes that occur across many industries. Top companies make use of them to get the best outcomes. When combined with good materials, it yields great outcomes.
This article will guide you on PMMA, which is a material used to make industrial products. There is a general question if you can injection mold PMMA. Well, the article will answer that and more. It will briefly introduce you to PMMA, explain what the material entails and is used for. It will tell you about the injection molding process, and how to injection mold PMMA.
What is PMMA?
PMMA stands for polymethyl methacrylate, it also means plexiglass. This is an alternative to its long and complex name. It’s a lightweight synthetic polymer, often seen as an alternative to polycarbonate. PMMA is not the strongest material, mainly used in products that don’t require high strength.
Historically, a German chemist O. Rohen discovered the PMMA in 1902. Poor surface hardness, poor resistance to impact, prone to scratching, and poor mold fluidity, these problems affect its usage a lot. But scientists have found ways to bypass these nowadays.
They modified PMMA materials by adding more substance to the parts of PMMA. One example is adding styrene and butadiene to it. Another example is adding PC.
Features of PMMA!
With regard to the molding process, you can mold PMMA using many processes, like casting or mechanical processing. And you can mold through injection molding. In this article, we’ll focus on injection molding. Processing PMMA by injection molding allows you to produce in numbers. But first, what are the features of PMMA?
PMMA absorbs water. It has an absorption rate of about 0.3-0.4%. Its ability to absorb water does little damage though, the presence of water reduces transparency in PMMA products and causes defects such as bubbles, gas lines. Therefore, we need to do dry it before processing PMMA. Dry processing helps avoid all these damages. The dry processing is under 80-90°C temperature, and mostly keep it for over 3 hours.
With PMMA you might be able to use recycled materials. But be careful! The quantity needed depends on the required quality. Ensure that the recycled material has no contamination, for contamination can affect the transparency of the item. It also affects the quality of the item.
For melt rate, PMMA is very sensitive. A slight change in the injection temperature can change its rate. But Compared with ABS or PS, it has a lesser flow generation. These are some features of PMMA. Understanding these helps with the general knowledge of injection molding.
What is the injection molding process?
A major production process is injection molding. It is the process of injecting material into a mold after heating such material. It is a famous process used for mass production.
You can use it for ABS, PS, and PMMA. Using this process, you can shape material as you desire, and create products in large numbers with limited effort and less time. It is cost-effective.
Can you injection mold PMMA?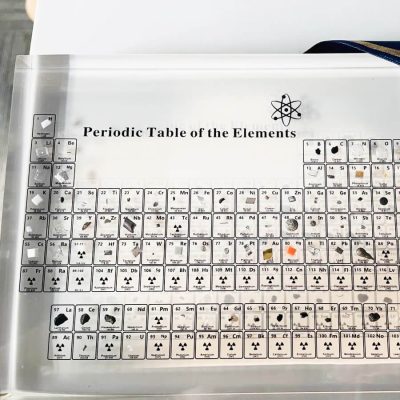
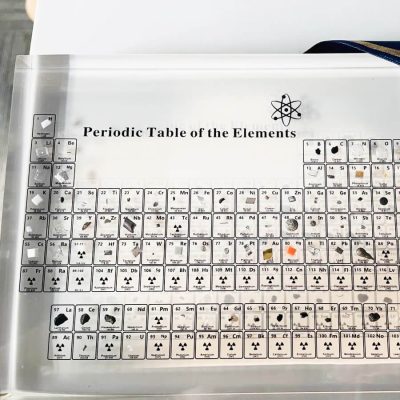
You may ask, can you injection mold PMMA? Well, yes you can. Just like other materials, you can injection mold it. When creating many items from PMMA use injection molding, this will ensure that you get top results.
Still, injection molding is a delicate process. The little details are vital. A little mistake can ruin the whole process, or ignoring one detail can make the process wrong. So, when injection molding, be careful. Thus, we will highlight some key details things to look out for while injection molding PMMA.
What to look out for in the PMMA injection molding process?
For every molding process, the material determines a lot. Its features and parts determine even the machine used. This helps to reach a top result. And PMMA also has some features to consider.
Nozzle and groove
Although PMMA doesn’t require any special injection machine, it has other requirements for top outcome. For instance, you need a deeper spiral groove and also a larger nozzle hole. This is because of the high viscosity of the material.
Strength and absorption
Also, consider the desired item. If it requires more strength, then, you need a special screw. One is with more diameter length to do the low-temperature plasticizing treatment. This would help give a better mix and strength.
Remember, what we said about PMMA absorption rate. It absorbs a lot of water. So, ensure you dry store it to prevent damage through water-absorbing.
Temperature and diameter
In injection molding, the temperature is very important. It can make good or ruin your mold process. So, for PMMA, set the temperature at 60- 80°C. This would help for a good melt and mix. Also, consider the diameter of the runner. The runners are vital systems in this process. Set your main runner to 8-10mm. With a gate lessee than 50mm, this gives a proper mix and prevents spilling.
Thickness
But the diameter depends on the features of the product. The thickness of the product determines the diameter. You have a runner with a diameter of 6-8mm.
Gate
With regard to the gate, you have options. Using proper gate size is vital. To get top products, you have the depth gate and fan gate. The first comes in at 0.7-0.9t. And the second has the same value.
There is the TAB gate of the mold. This comes in at 0.7 to 0.9t. Know that “t” means the wall thickness of the item.
There is the needle gate. It should have a diameter of 0.8 -2mm. This is larger than all the other gates. These are the values for your gate in this process.
Injection speed
Next to consider is the injection speed. This is the rate of injecting the material into the mold. It is the speed of injection into the mold. It can shape the quality of the product and the appearance of the product. It can even shape the quality of the mixture. So, the speed is crucial. And you cannot ignore it except you do not want a good outcome.
For PMMA, you can use the fast injection method. But remember to avoid internal stress. For it will ruin the material quality. You can also modify the injection speed. That is, adjust it for each stage of the process.
You can use a multi-stage injection process. This allows you to have both fast and slow injections at different levels of the injection process. For items with thick walls, use a slow speed. But otherwise, you can use slow-fast-slow speed mixing all together for a better outcome.
Retention
Up next is retention. The retention time is the time between stages when the resin leaves the first injection to the next. For this part, the temperature is vital.
For a temperature of 260 °C, 10 minutes is retention time. Or rather it should not go beyond 10 minutes. But when the temperature is about 270 °C, the retention time should not go beyond 8 minutes. So, the higher the temperature, the lesser the retention time. And the lower the temperature, the higher the retention time.
Also, you should measure the air injection-based which would be based on the melt temperature. And for PMMA that is around 210- 270°C.
Conclusion
That is it, your brief introduction to PMMA. Now you know what PMMA injection molding is. And can boldly discuss or conduct the molding process. So, read over this article if you need to. But ensure you keep hearting all the details as they will help in your production process.
Remember, the features of PMMA. It absorbs water. It has bad surface hardness. It is very poor with impact resistance. And has poor fluidity. But still, it is a good production material. For it is lightweight. It is easy to mold. And it is cheaper than others. It has good electric parts.
So, companies use it for many products. Such as car lights, parts of instruments. Transparent pipes, and even optical lenses, and when they want to produce in large numbers. These companies use the injection molding process which works well with PMMA.