Aerospace is one of the complex and critical industries where stringent quality measures are taken during component manufacturing. That’s because the safety of passengers and aircraft is dependent upon precise components.
Even a small deviation could result in catastrophic failure. So, the stakes are high and machining tolerances are tight to ensure that every manufactured part fits right in and performs well.
Read this article to learn about the accuracy requirements and standards followed in aerospace component manufacturing.
Accuracy Requirements in Aerospace CNC Machining
Aerospace components operate under extreme conditions, such as high pressure, intense heat, and high-stress forces. That’s why each component needs to be manufactured with utmost accuracy to seamlessly work in such critical environments.
Precision Requirements for Different Aerospace Parts
The tolerances and precision requirements vary between ±0.005 to ±0.0001″ across aerospace components.
The aircraft’s structural components, including fuselage frames, wing spars, and tail assembly, are subject to high load during the operation. Plus, they are an assembly of multiple components that need high precision to fuse. For such components, the tolerance levels are ±0.005 to ±0.002″.
Engine components like turbine blades and rotors require the tightest tolerances, often in the ±0.0001″ range. Since these parts operate at high speeds and temperatures; thus, any deviation could lead to inefficiencies or hazardous failures.
Aircraft control surfaces (such as flaps, ailerons, and elevators) manage the aircraft’s aerodynamic stability. Precision is critical here too for responsiveness and control. Their tolerance levels are up to ±0.002″.
Surface Finish Requirements
In aerospace components, 8 µin Ra is the standard surface finish. However, for some critical rotating components in aerodynamic machinery, it can be as low as 0.25 µin Ra.
Role of CNC Machining Operations in Accuracy Requirements
Each aerospace component is produced through a machining operation or series of operations. The precision of each operation is limited and it is reflected in the final tolerances of parts.
Precision CNC Milling
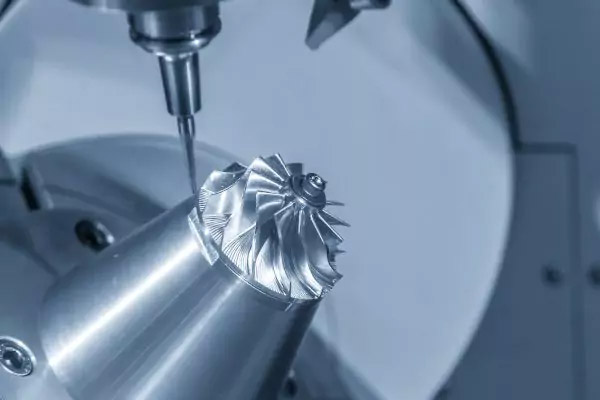
Source: BoyinCNC
CNC milling is used for complex parts with detailed features, such as airframe components, brackets, and housings. The milling machines are versatile and capable of handling both large and small components.
Advanced multi-axis milling machines (3-axis, 4-axis, and 5-axis) offer extreme precision, with tolerances as tight as ±0.0001″. In these machines, the cutting tool can move and cut at different angles and positions, achieving complex geometries with minimal error.
CNC Turning
Source:Dekmake
CNC turning is primarily used for cylindrical and symmetrical parts like shafts, landing gear components, and engine cylinders. In this machining operation, the workpiece rotates while a cutting tool shapes it. CNC turning centers, particularly multi-axis turning centers, can achieve tolerances as tight as ±0.005″.
Wire EDM Machining
Wire EDM uses an electrically charged wire to cut the material with extreme precision. It is used for machining hard-to-machine metals (tungsten) and creating complex internal geometries that may not be feasible with milling.
Turbine blades, fuel injector nozzles, and control mechanism components are made through EDM. It is common for Wire EDMs to make parts with accuracy up to 0.0001″.
Laser Cutting
Surface Finishing Techniques for Aerospace Components
Although CNC machines have a role in achieving precise parts, the fine tolerances are primarily subject to the final surface finish. To fine-tune and smoothen out machined parts, the following surface finishing techniques are quite popular:
Anodizing
Anodizing is an electrochemical process that converts the metal surface into a durable anodic oxide finish. It is basically done on Aluminum parts to colorize them and enhance their wear resistance. Among parts, brackets, and housings are usually anodized.
Powder Coating
Powder coating is a finishing process where a dry powder is electrostatically applied to a surface and then cured under heat. This creates a hard, protective layer that is both aesthetically pleasing and durable.
HVOF Coating
HVOF (High-Velocity Oxygen Fuel) coating involves spraying molten or semi-molten material onto a substrate at high velocity using a combustion process. This results in dense coatings with excellent adhesion. It is commonly used on turbine blades in aerospace engines.
Electroplating
Electroplating is a process that uses electrical current to deposit a layer of metal onto a substrate. Common finishes include nickel plating for corrosion resistance, chrome plating for shine and durability, and gold plating for electrical components. Fasteners and connectors in aerospace systems are usually electroplated.
Overview of Aerospace Manufacturing Standards
The design and tolerances of aerospace parts are subject to some standard practices. These international standards govern the quality and dimensional accuracies of aerospace parts:
AS9100 D
AS9100 D is a widely recognized quality management standard specifically for the aerospace and defense industries. It builds on the ISO 9001 framework but includes additional requirements tailored to aerospace needs, such as risk management, product safety, and continuous improvement.
ISO 12573:2010
ISO 12573:2010 provides guidelines for the assessment of the dimensional accuracy of mechanical components. This standard focuses on the measurement methods and techniques used to evaluate the accuracy of manufactured parts, ensuring that they meet specified tolerances.
ASME Y 14.5
ASME Y14.5 is a comprehensive standard that defines the system of Geometric Dimensioning and Tolerancing (GD&T) used to specify tolerances for the shape, orientation, and position of parts.
How RJC Mold Can Help in Aerospace Component Manufacturing
RJC Mold is a trusted partner in aerospace component manufacturing. We have been offering comprehensive CNC machining for the past two decades. Our products meet the ISO 9100D standards, ensuring the quality of our products is at par with the industry.
Besides machining, we also offer injection molding, mold making, sheet metal fabrication, and 3D printing services. Our team can handle your project from concept to production. Contact us today and let us know how we can space.