Powder Metallurgy
Rjcmold in delivering custom powder metal parts and components. With a fully integrated manufacturing facility, we use powdered metal technology to provide at or near net shape parts that are custom-engineered to meet your specific needs. We can work with you to design the ideal part that offers the highest performance and quality for your application while maintaining cost-effectiveness.
Rely on Rjcmold for Your Powdered Metal Parts
Powder metallurgy is a highly efficient, versatile, and affordable process that can deliver a range of complex parts while maintaining tight tolerances. Because of its many benefits, industries of all types rely on powdered metal parts for various applications.
If you need reliable, high-quality powdered metal parts or components for your project of Rjcmold, is your ideal partner. We can work with you from beginning to end to create a fully customized powdered metal solution that meets the unique requirements and specifications of your application. With our comprehensive services, we can provide design and engineering assistance as well as precision manufacturing processes to provide powdered metal parts that exceed customer expectations.
For more information about our custom powdered metallurgy capabilities, or to get started on your powdered metal solution, request a quote today.
Cost Effectiveness of Powder Metallurgy Manufacturing
Cost effectiveness is one of the key advantages of powder metallurgy processes. When compared to traditional manufacturing methods, powder metal manufacturing requires less energy, makes better use of the material, and requires less steps to produce a finished product. Many of the materials used today are made by melting scrap metal and using some highly specialized processes to make the powders. Because powder metal processes are so repeatable, the cost effectiveness increases with higher volumes. Once the parts are set up in the press, robots transfer the parts directly to the sintering furnace, reducing the need for handling and ensuring the parts off the press are handled with care. When production volumes require automation, parts can be taken from start to finish with very little operator contact. Today’s powder metal technology can also reduce or eliminate the need for machining. Pressing technology and mold design capabilities allow for many specialized features to be formed at the first step in this advanced manufacturing process and the net result is less machining, and that translates into less waste.
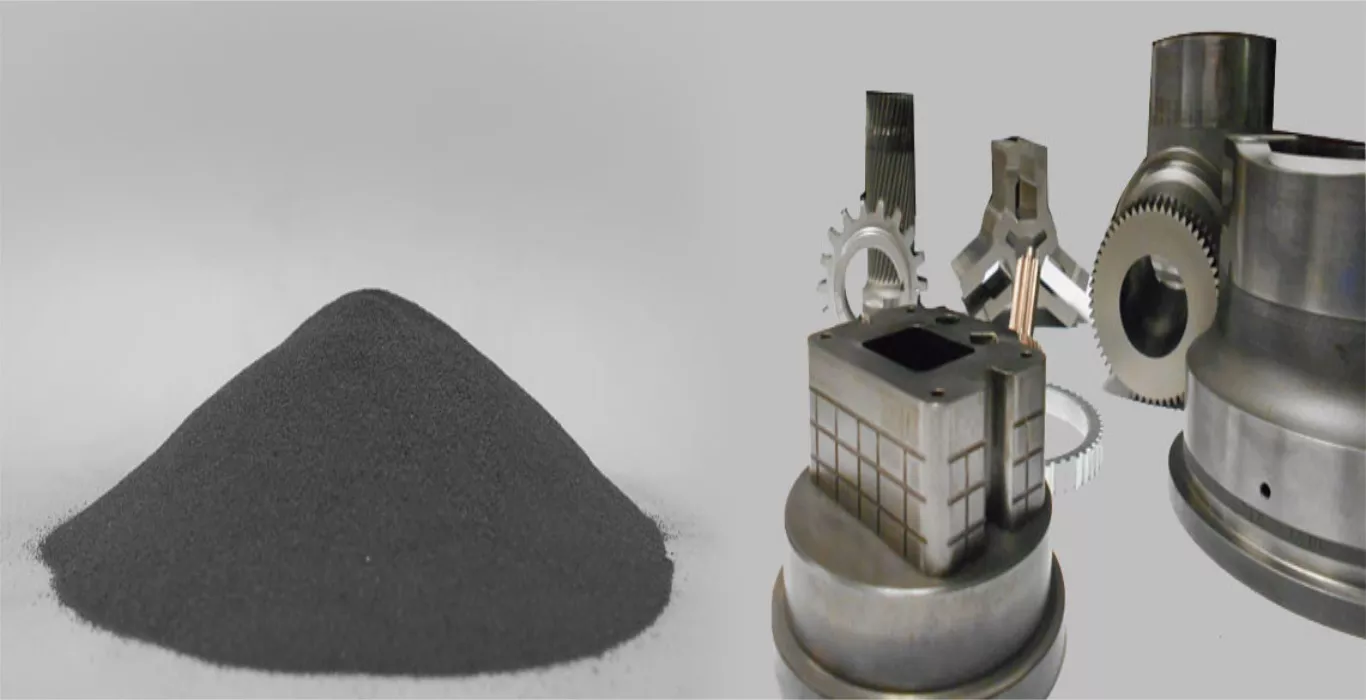
Advantages of Powder Metallurgy Technologies
Powder metallurgy provides a range of benefits in various applications. Parts and components made with powder metal often exceed the quality of parts made with other metallurgy techniques. The primary advantages of powder metal technologies include:
- Improved versatility, flexibility, and uniformity
- Cost-effectiveness
- Produces high-quality parts with a longer life cycle
- Ability to produce high part volumes
- High-quality surface finish
- Ability to improve wear resistance and strength through heat treating processes
- Minimized material waste
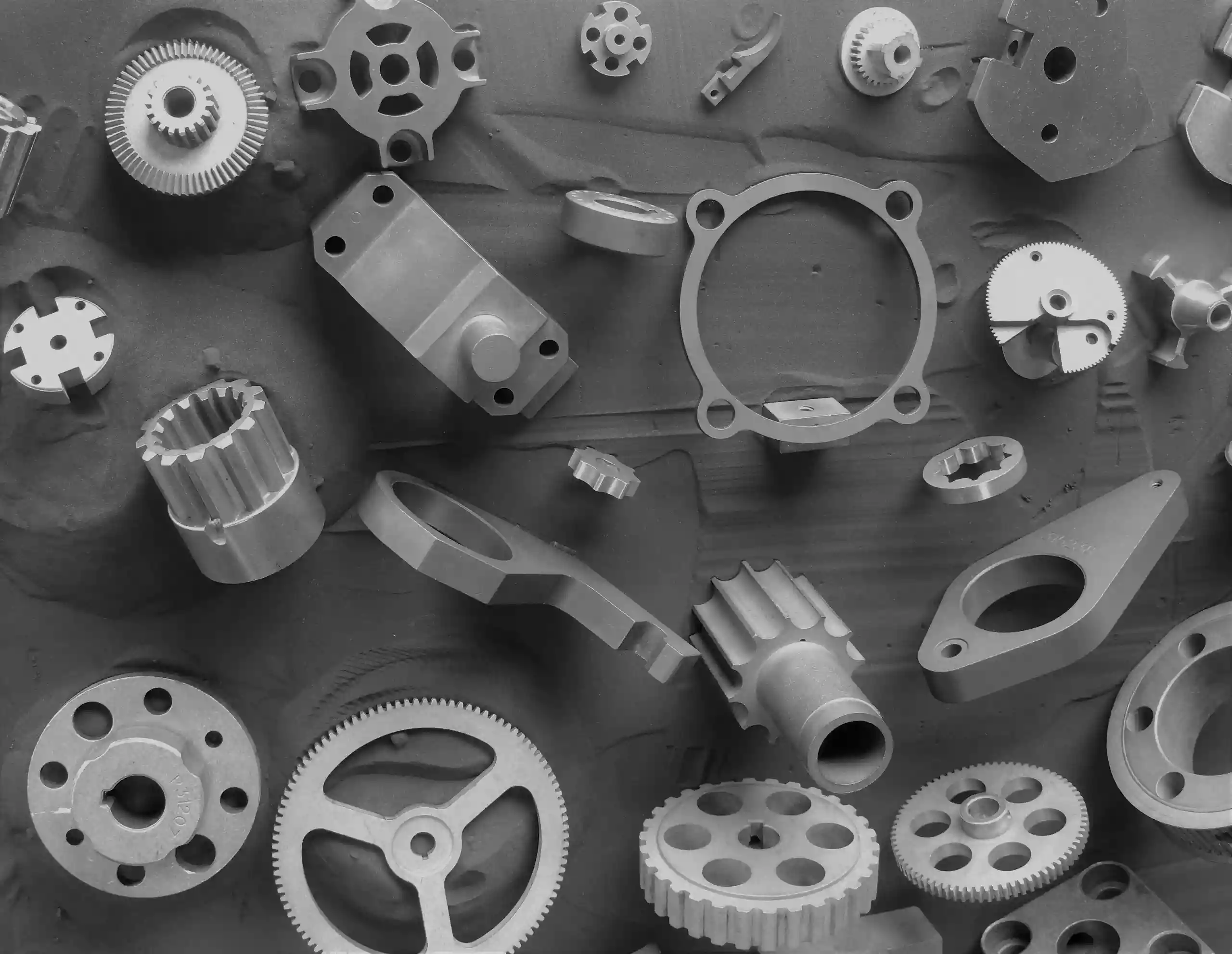
Powdered Metal Parts Within Rjcmold
When partnering with Rjcmold for powdered metal parts, we guide the client through each stage of the manufacturing process, including design, material selection, finishings, production, inspection, and shipping. Our highly streamlined process ensures optimal speed and cost-effectiveness for your powdered metal project.
Rjcmold serves various industries with quality powder metallurgy services, including structural, recreational, power transmission, material handling, marine, lawn and garden, fluid handling, food service, electromagnetic, automotive aftermarket, and agricultural applications. With decades of experience producing custom metal parts and components, we offer comprehensive services to ensure the most economical and appropriate powder metal solution for your specific application.
Design Considerations
- Part must be so designed to allow for easy ejection from the die. Sidewalls should be perpendicular; hole axes should be parallel to the direction of opening and closing of the die.
- Holes, even complicated profiles, are permissible in the direction of compressing. The minimum hole diameter is 1.5 mm (0.060 in).
- The wall thickness should be compatible with the process typically 1.5 mm (0.060 in) minimum. Length to thickness ratio can be upto 18 maximum-this is to ensure that tooling is robust. However, wall thicknesses do not have to be uniform, unlike other processes, which offers the designer a great amount of flexibility in designing the parts.
- Undercuts are not acceptable, so designs have to be modified to work around this limitation. Threads for screws cannot be made and have to be machined later.
- Drafts are usually not desirable except for recesses formed by a punch making a blind hole. In such a case a 2-degree draft is recommended. Note that the requirement of no draft is more relaxed compared to other forming processes such as casting, molding etc.
- Tolerances are 0.3 % on dimensions. If repressing is done, the tolerances can be as good as 0.1 %. Repressing, however, increases the cost of the product.
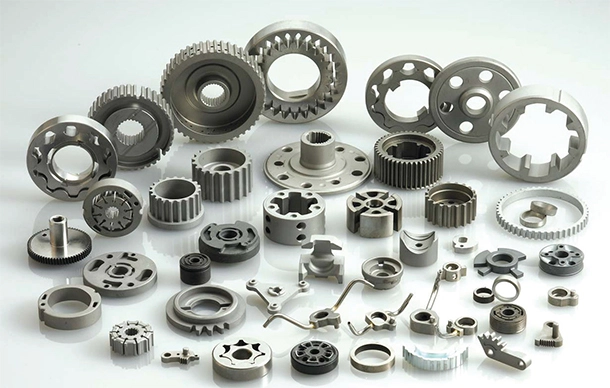
Secondary Operations
- The application of finishing processes to the sintered part. In the Powder Metallurgy industry, such processes are often referred to as “secondary operations”.
- Sizing – Sintering may produce small dimensional changes in the compacts. Therefore, parts with very close tolerances, are sized in seperate tools.
- Oil Impregnation- The parts are impregnated with oil through a vaccum process.
- Heat Treating – This is the heating of a sintered metal part in a protective atmosphere and then oil quenching the part. The results are usually improved strength and hardness.
- Machining – If required powdered metal parts can be machined to obtain the desired shape before or after heat-treating is completed.
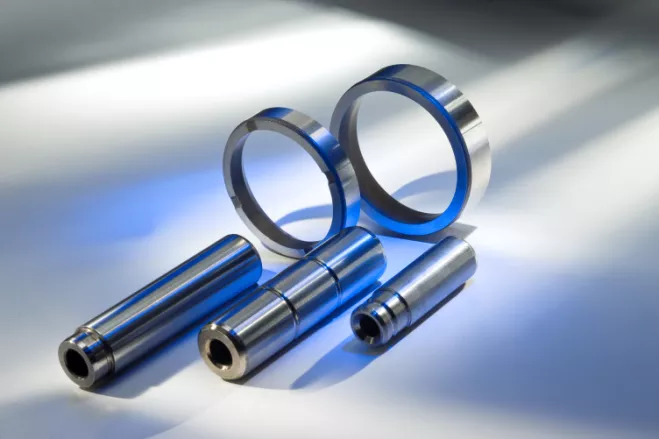
Custom Manufactured Powder Metal Parts and Components
Rjcmold began making powder metal components in the 2003’s and has since grown into a world-class company in the powder metallurgy industry, offering products across a wide range of industries and/or markets. Powder metallurgy manufacturing produces parts for a diverse range of industries, and it often offers designs or features not available or not cost effective with traditional manufacturing. Powder metallurgy designs can reduce weight and include additional features while cutting down on the amount of waste generated by the manufacturing process.
Wondering how powder metallurgical engineering can help your project? Let our team at Rjcmold take a look and find out what powder metallurgy can do for your business.