Rapid Injection Molding & Tooling Services
Rjcmold provides aluminum mold and steel mold for rapid tooling according to the needs of customers. It can hand over the parts of your designated materials within 2-5 weeks. From functional prototyping to low volume production to mass production of parts, we combine rapid injection molding advanced equipment with proprietary technology and experienced manufacturing teams to provide high quality injection molding parts, so as to help you reduce design risk and save overall production cost.
Rapid tooling on the Rjcmold
Rapid tooling is a manufacturing process that uses special techniques and technologies to quickly and efficiently produce high-quality production tools. This can include the use of 3D printing, CNC machining and other advanced techniques to quickly produce moulds, dies and other types of tools.
One of the main benefits of rapid tooling is that manufacturers can quickly and easily produce custom tools and parts that can be used for a variety of applications such as prototyping, testing and low-volume production. This reduces the lead times and costs associated with traditional tooling processes and allows companies to bring new products to market faster.
In addition to speed and versatility, rapid tooling is also very accurate, producing tools with high precision and repeatability. This makes it ideal for producing complex and intricate parts and ensures that the end products meet the highest quality standards.
Producing tools and tool inserts directly from 3D data is no problem with the Rjcmold rapid tooling service. Here you can have items such as tool inserts for injection molding or vacuum casting manufactured quickly and economically in real materials.
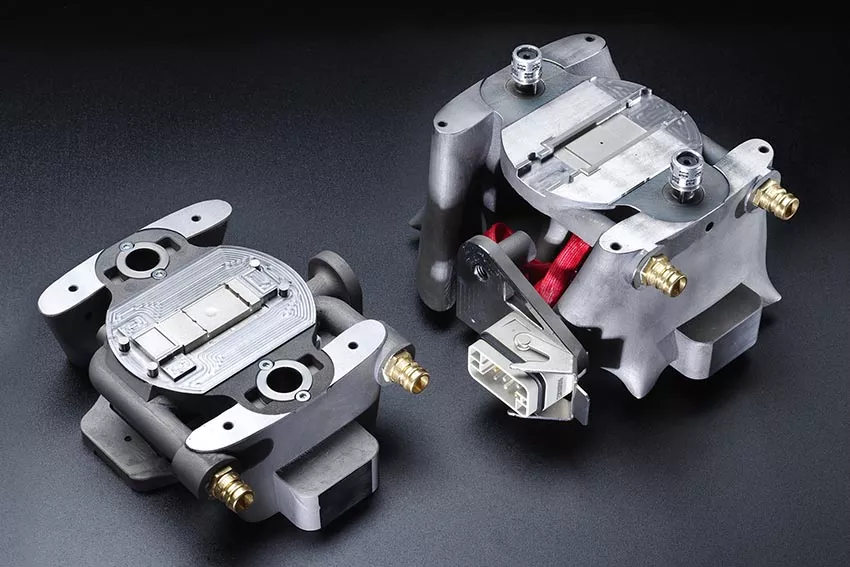
What is rapid tooling?
Rapid Tooling is when Rapid Prototyping techniques and conventional tooling practices are used together to produce a mold quickly. This process is also used to prepare parts of a model from CAD data in less time and at a lower cost compared to traditional manufacturing methods. Rapid Tooling is used as a channel to produce injection molded parts.
Capabilities in die build
Rapid Tooling Systems designs, builds, and services small to medium sheet metal stamping dies.
With a wealth of experience, Rapid Tooling Systems specializes in:
- Progressive dies and high speed progressive dies
- Compound dies
- Large packages of dies
- Die tapping and nut unit progressive dies
- Line dies
- Draw dies
- Transfer dies
- Engineering change support
- Die repair support at our facility or at our customer’s facilities
- Short lead time builds
- Extrusion progressive dies
- Electrical terminal progressive dies
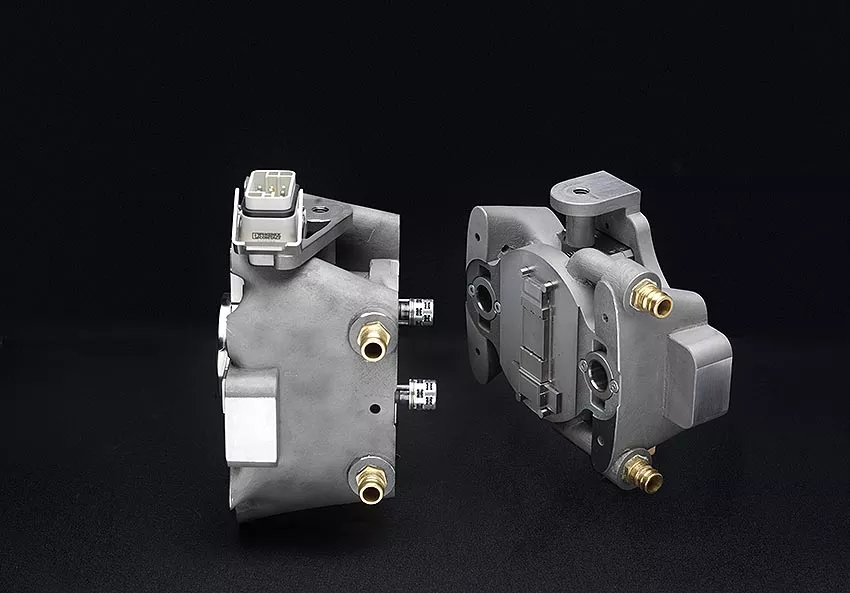
What Rjcmold Offers
Rjcmold offers two different types of rapid tooling: prototype/bridge rapid tooling and short run/production rapid tooling.
Prototype/Bridge Rapid Injection Molding & Tooling for quantities from 50 to 2,000
Typical applications:
- Validate part design
- Validate material selection
- Validate tooling concepts
- Limited product life span
- Supply parts while production tooling is being manufactured
Short Run/Production Rapid Injection Molding & Tooling for quantities from 1,000 to 100,000
Typical applications:
- Finalized part design
- Defined material requirements
- Defined manufacturing quantities
What engineering and design services can we provide for the rapid tooling?
rapid tooling 3d drawingAs to minimize the molding problems, we need to review the 3D model structure design and confirm the tooling building feasibility. The potential quality problems need to be eliminated as much as possible before cutting steel. We offer a reliable solution for our client to address molding issues:
DFM (Design For Manufacture): This report is a very helpful way to show the mold layout and product information, which include part color, part finish requirement, gate type and location, parting line, ejector pins location and other information. We can provide the DFM report in one or two days based on the complexity of the product structure.
- Product Structure Optimization Proposal: If we find any structure design that is not suitable for the tooling building or if there is potential quality risk in the current product design, we will provide you proposals to optimize the design structure.
- Product Design Assistance: If you have a product idea, we can help you transfer ideas into the 3D model. If you need engineers to change your 3D models, our designer team can help, too.
- Mold Flow Analysis: RJCmold can also make mold flow analysis report if needed.
- Mold Design Detail: We can provide the core and cavity inserts design detail of the tooling design.
Controlling Costs and Lead Times
With design, tooling and moulding all on one site, our experienced toolmakers and design team offer clients rapid tooling, faster lead times and uncompromised quality.
We understand that outsourcing plastic manufacturing overseas can often mean missing deadlines, poor workmanship, expensive hidden costs and unwanted setbacks.
That’s why our experienced, China based team are proud to provide a high quality, efficient plastic production service for customers every time, wherever they are in the world.
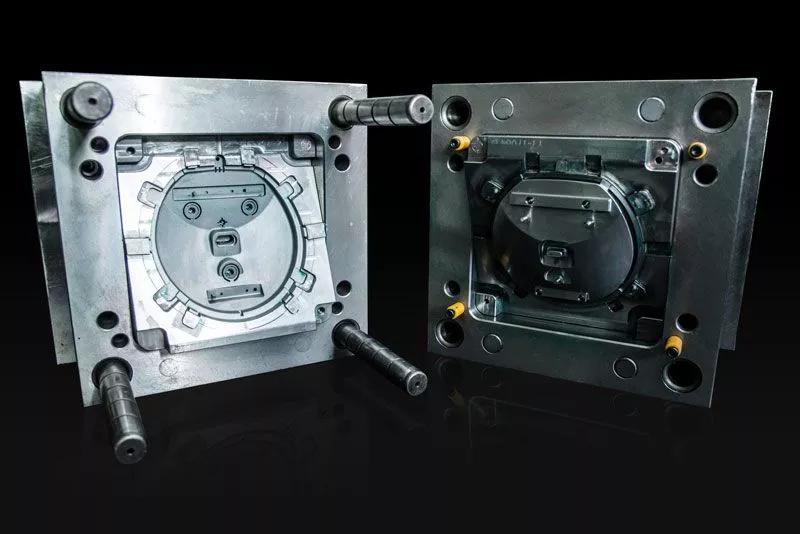
What is the advantages of rapid tooling?
- Reduce 40~50% cost compared with the traditional mold.
- Reduce 40~60% lead time compared with the traditional mold.
- The mold can be available for various of surface finish, such as: Texturing, Polishing, Sand blasting, etc.
- Soft steel make it easier to modify the tooling if the product design need to be changed.
- The mold can be made as family mold, so it can reduce the production lead time and keep the color consistency of the products.
- Rapid tooling is a good testing solution prior to huge volume production mold.
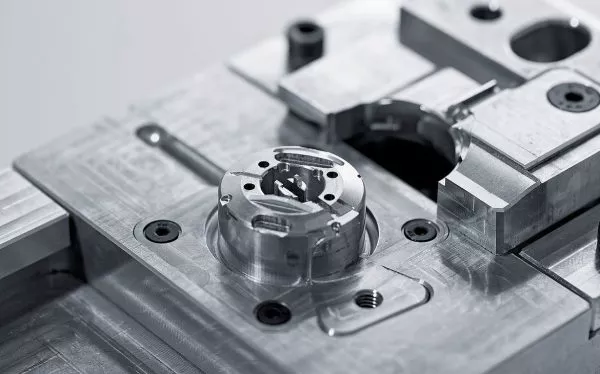
Request Your Rapid Tooling Quote Today
Our improved algorithm decreases rapid tooling quotation times by up to 90%. Most quotes are delivered within 24 hrs. and usually much less, depending on project details. Your customer support partner will contact you directly to ensure you’ve received and understand all aspects of your quotation and to answer any questions you may have.