Automotive plastic parts manufacturer
When you partner with RJC, you align with a seasoned provider of plastic injection molding services, including injection molding, insert molding, over-molding, and micro-molding. You may also take advantage of our multi-shot plastic injection-molding capabilities for the automotive market.
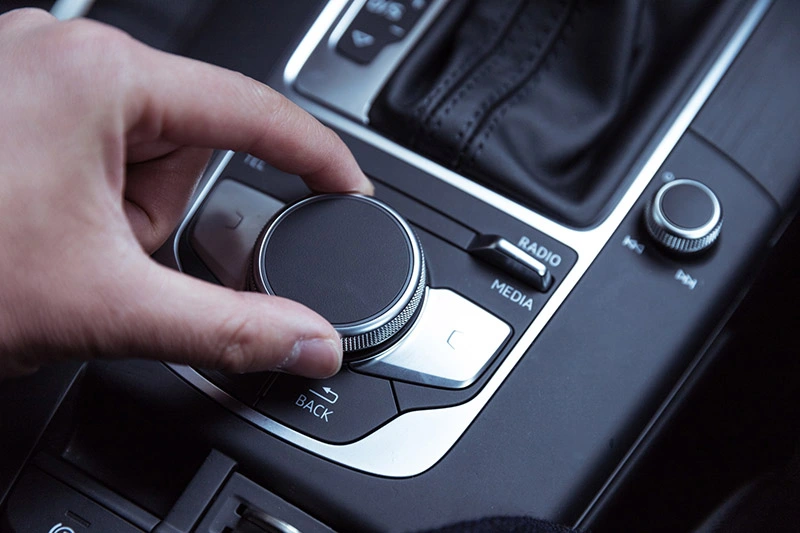
Mold Show
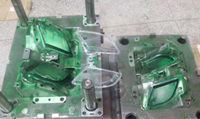
RJC Automotive Lighting Mold
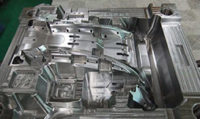
Automotive Mold
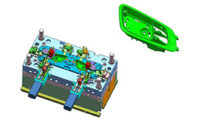
Auto Interior Mold
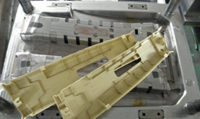
RJC Automotive Mold
Products
Cooling Fan
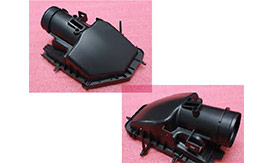
Auto Engine Part
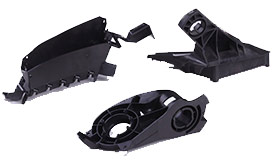
Auto Structural Part
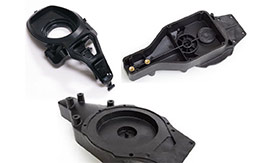
Auto Part Insert Molding
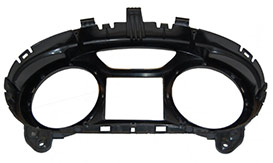
Auto Dashboard Mold
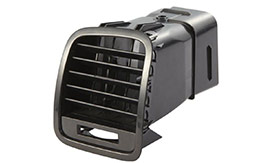
Air Vent product
Our Automotive Injection Molding Process
At RJCMOLD, we have an experienced, knowledgeable team, including product designers, plastics engineers, and manufacturing factory. all working together to ensure you get the custom molded plastic components and automotive parts you need. We’ll sit down with you to discuss the specifications of your project, including the product you need, how it will be used, the quantity, and other important details. Using this information, we can help you decide whether automotive thermoforming or automotive injection molding is the best option, as well as the right thermoplastic to use.
With the details finalized, we can then produce a highly detailed three-dimensional model of the product and print it out with our innovative 3D printing technology to create and test a prototype. Our team will work with you to make any necessary adjustments, troubleshoot any concerns, and look for opportunities to improve the design.
Once the prototype is complete and has your approval, we can move to the tooling phase, where we design the complex, double-sided injection molds used to shape and form the products, parts, or components. Because automotive plastic injection molding requires precision and perfection, we will also produce temporary tooling to determine the proper pressure needed, troubleshoot any concerns with the mold, and ensure the end result is accurate to the design and product prototype.
once the design is finished,we are able to begin the plastic injection molding process for your automotive parts. Thermoplastic material is heated to a liquid and, using injectors able to produce up to 1000 tons of pressure, the melted plastic is injected into the cavity, coating the interior of the mold and filling it to capture every detail, corner, and angle. After the plastic cools, it is ejected from the injection mold and is sent for any finishing tasks, including sanding, painting, or assembly.
Interior injection molded car components
To the dynamic automobile industry we are a reliable partner in production of a variety of injection molded interior components. In our ISO IATF accredited factories we carry out interior component projects for the leading automotive manufacturers. We are experienced OEM, Tier 1 automotive supplier and manufacturer of automotive interior and exterior trim parts. Our product portfolio of interior injection molding components comprises plastic auto parts such as: dashboard elements (e.g.: glove compartment, door and window pillars), steering column trims, door handles, air vents, centre consoles, roof modules, etc.
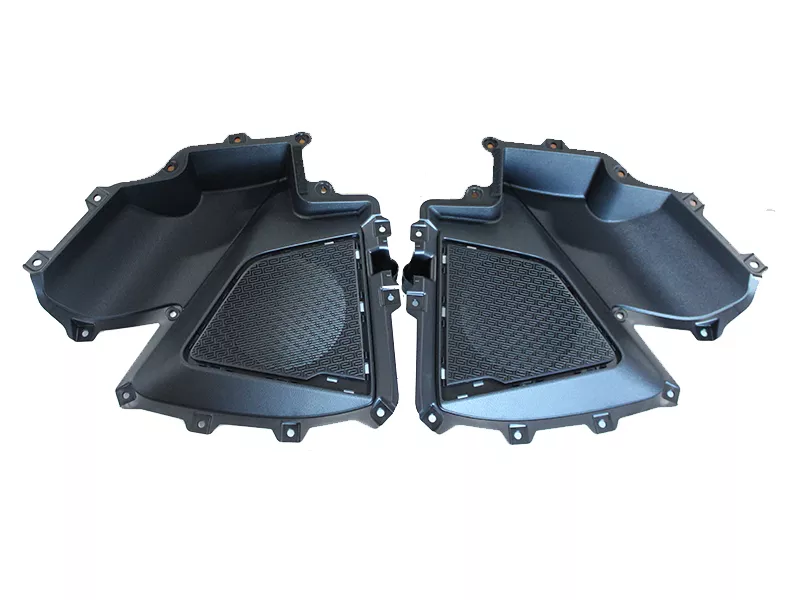
Exterior injection molded car components
Injection molding is the ideal technique to manufacture a broad range of exterior car components. Our team of experienced injection molding professionals works closely with automotive OEMs and Tier 1 clients to evaluate and define all technical requirements and therefore optimize the production of impeccable exterior vehicle components. We are plastic injection molding manufacturer of automotive exterior parts e.g.: mudguards (fenders), wheel arches, grilles, sensor holders, floor rails, trunk trims front and rear coverings, bumpers and exterior car door trim, door panels. Our injection plastic parts for cars are found in the a variety of car models worldwide.
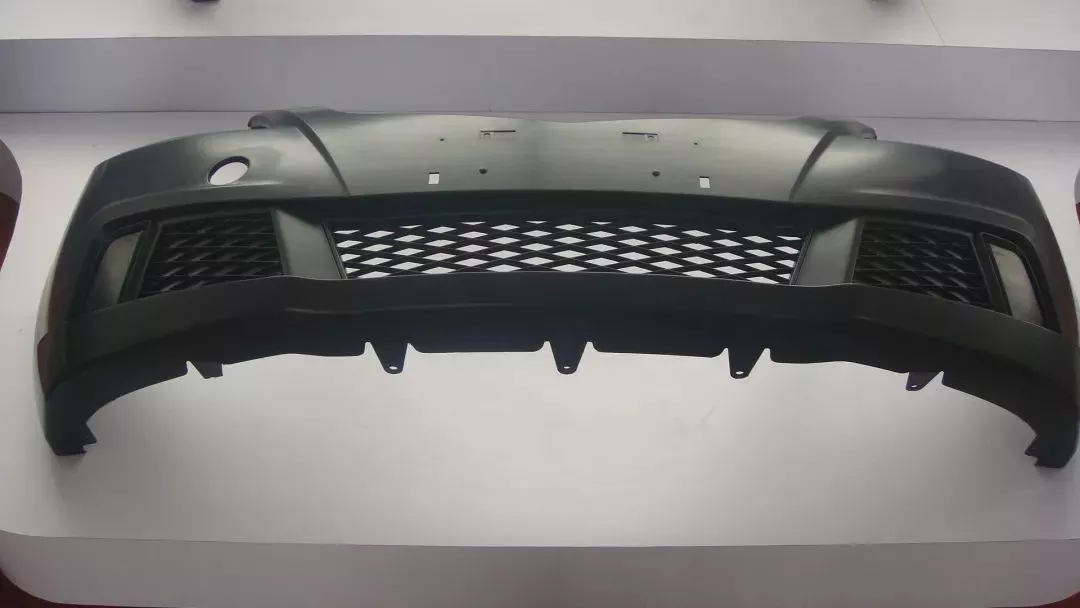
Why Choose Custom Automotive Plastic Injection Molding
The automotive industry is choosing custom plastics over metal or ceramic parts at a higher rate than ever because today’s engineering-grade resins and polymers are lightweight, durable, and high-performing, able to withstand extreme heat and friction. By using plastics, vehicles have improved fuel efficiency, are less expensive to produce, and the exterior elements are more impact and scratch-resistant to their ceramic or metal counterparts.
Because the double-sided tooling used for automotive plastic injection molding is more complex, it has a longer lead time than thermoforming, usually 16 to 20 weeks rather than 14 weeks. However, there are several benefits to choosing injection molding automotive parts.
High Volume Orders
In order to withstand mass-producing plastic car parts, our tooling is made from heavy gauge steel, aluminum, or beryllium-copper alloy. Whether you need a single, high-volume production run or multiple orders, being able to re-use the injection mold significantly reduces the per-unit cost of your plastic parts.
Fast Production
Once the automotive injection mold is ready for use, this process allows for rapid manufacturing. There’s minimal, if any waste, so once the plastic parts are out of the mold, they can be finished or assembled as needed.
Complex or Advanced Component Designs
Plastic automotive parts are often incredibly detailed with varying thicknesses, raised edges, and sharp corners or angles. An injection mold allows for these details in a way that can’t be obtained through other production processes.
Small Components
Body panels and large pieces can be formed through thermoforming, but knobs, dials, and other small automotive components are more easily produced through injection molding because we can create multi-cavity molds to speed up the manufacturing processes.
Automotive manufacturers are often met with parameters to improve safety, increase fuel efficiency and initiatives to promote sustainability.
At RJCMOLD, we want to deliver the best to our clients and we do this by providing our clients with affordable plastic parts and in-house made plastic injection molds.
We have successfully managed to create and optimize plastic parts that are strong and durable. Plastic parts are becoming increasingly popular and replacing metals in the automotive industry and the primary reason to choose injection molded plastic parts is weight reduction. This trend further increases with electric cars.
Partners in Automotive Part Design
and Material Selection
The demands placed on injection molded plastic parts within automotive applications are great. Designs are increasingly complex and sometimes require tolerances as tight as .001 inches. Harsh under-the-hood operating environments present extremes in temperatures, chemical exposure, and performance requirements. Designs and materials must stand up to the test.
Currently, there are more than 25,000 resins engineered to provide specific physical characteristics such as strength, flexibility, temperature, corrosion, and UV resistance. As material science and injection molding experts, RJCMold engineers share their in-depth knowledge to help automotive OEMs select the best plastic for performance and budgetary goals. This is apparent when designing and manufacturing complex parts and components for vehicle braking systems, cooling systems, fuel delivery systems, and the powertrain.
