Custom Medical Metal or
Plastic Parts
RJC has gained ISO13485: 2016 and FDA license and has supported injection molding clients in the medical equipment industry for years with rapid manufacturing services to help get products to market. We understand that the medical equipment components we produce are on the critical path for pre-production testing, validation and verification, and limited market release production.
Due to the importance of this role, we work very closely with our clients’ design and procurement teams at every phase of each project to ensure we deliver quality components according to a schedule they can count on. We also follow our streamlined production process to ensure the right people are in place, from design to part.
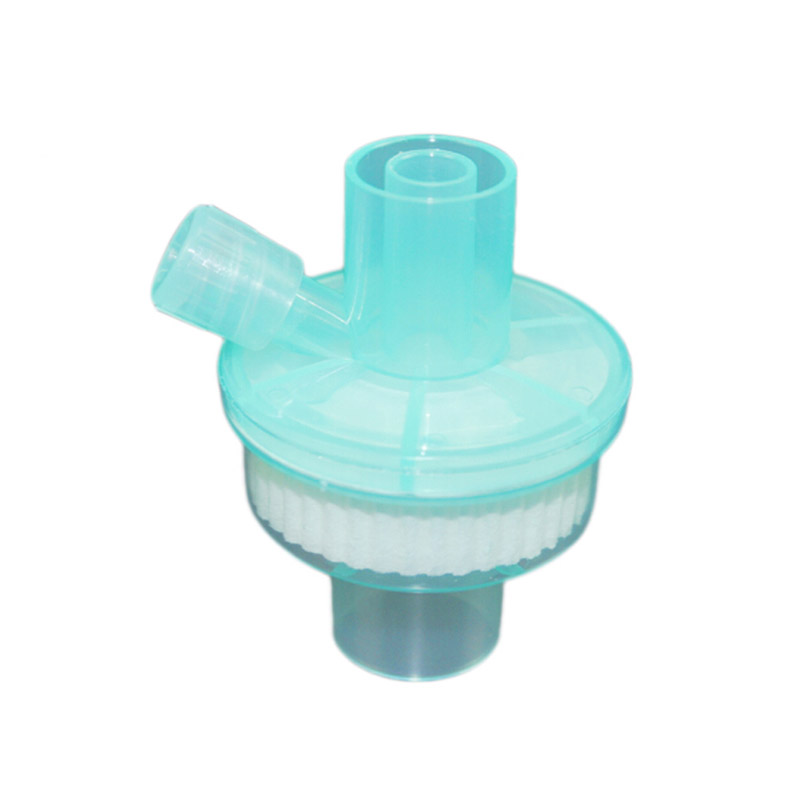
Medical Parts Mold
Medical Injector Mold
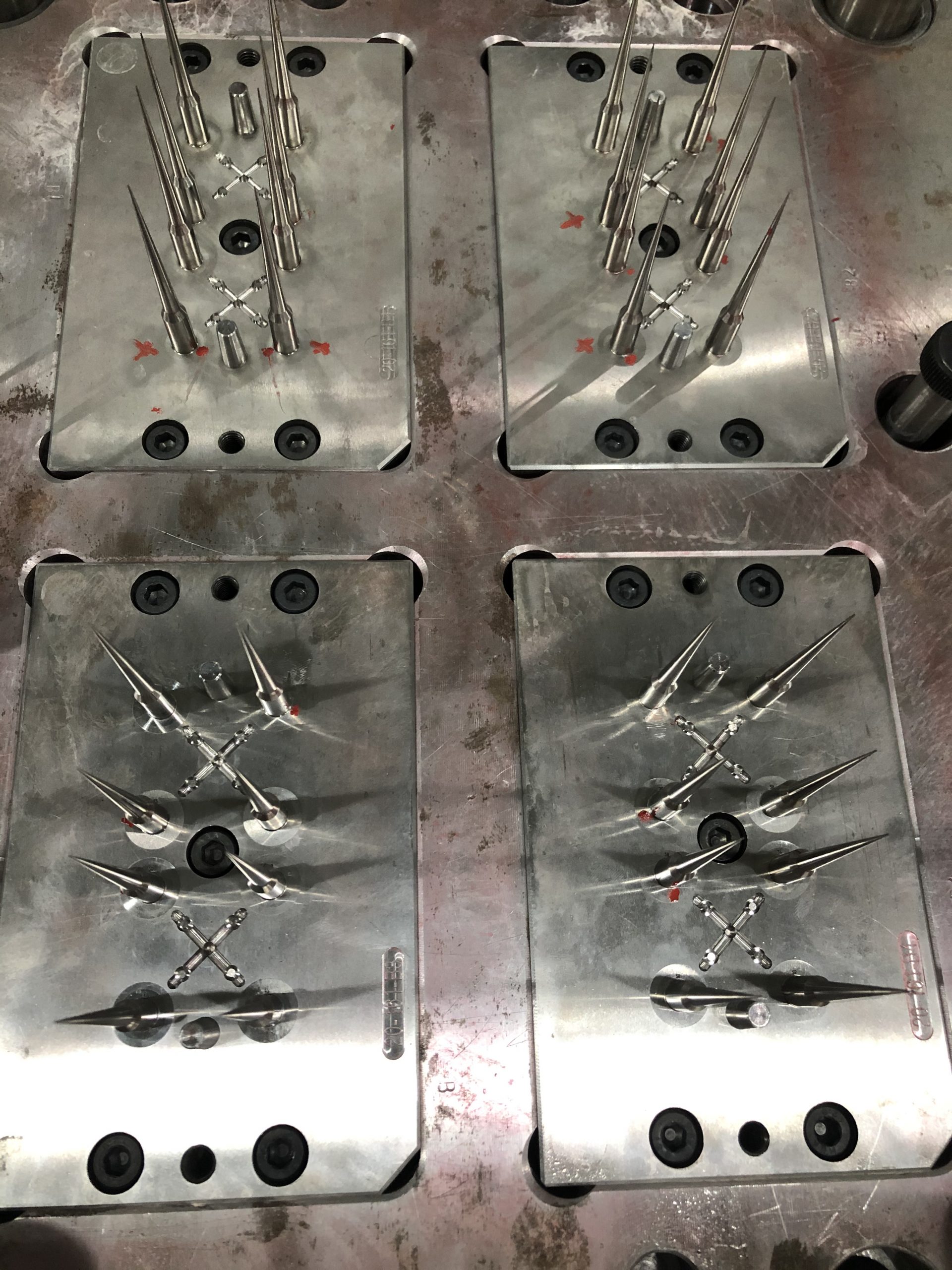
Medical Testing Tube Mold
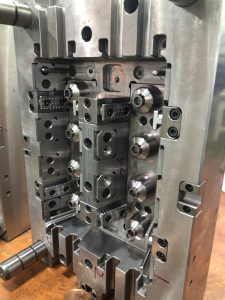
Medical Testing Tube 2K Injection Mold
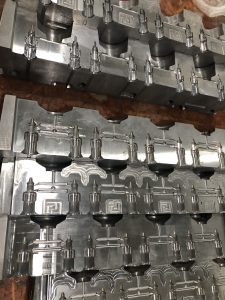
Medical Disposable Testing Tube 2K Injection Mold Core
Medical Products
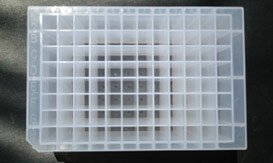
Medical Device

Medical Injector Tube
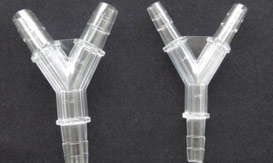
Injection Splitter Tube
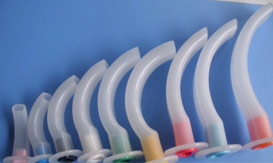
Medical Tubes Mold
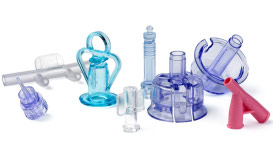
Medical Parts
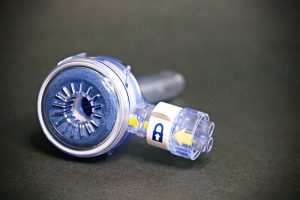
Medical Instrument Component part
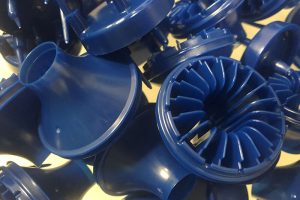
Medical Injection Molding Parts
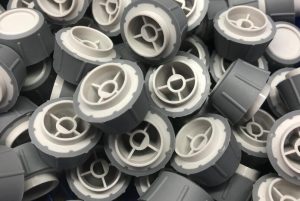
Medical 2K Injection Molding Parts
Molding Capabilities for Medical Devices
Our strength is helping our customers make complex parts that our competitors often can’t. RJCMOLD is certified to ISO 13485:2016, among other certifications, demonstrating our commitment to serving our clients. We offer:
- ISO 13485, ISO 9001, and AS9100D registered facilities
- ISO Class 8 and Class 7 cleanroom environments
- Both US-based and China injection molding for tooling and production
- Overmolding, insert molding, assembly, post-mold heat staking, and metal injection molding (MIM)
- Part sizes ranging from micro to 300 square inches
- Expertise with a wide range of materials used in medical molding, including PEEK, Ultem®, TPEs, Radel®, PSU, Delrin®, Lexan®, PEBAX®, ABS, and more.
- Urethane casting, liquid silicone rubber molding, CNC Machining,and 3d printing services are also available.
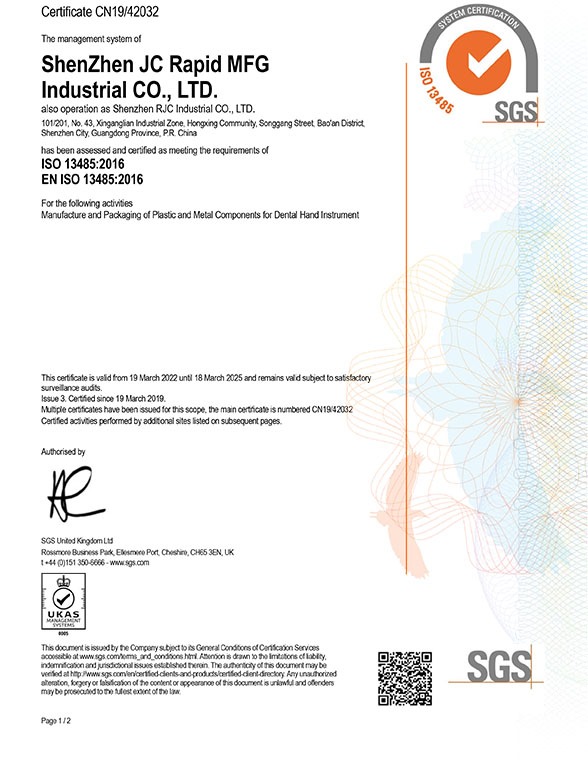
Get a Same Day Quote
Experts in medical injection molding, we remain focused on delivering high-quality components for patient critical devices utilized for Medication Delivery, Surgical Eye Care, Endoscopic Treatment, Digestive Health and more. Receive Your Same-Day Quote and Risk-Free Project Evaluation
Injection Molded Parts for the
Medical &
Pharmaceutical Industry
At RJCMold, we specialize in full-service, turnkey plastic component injection molding solutions. Our comprehensive part manufacturing capabilities allow customers to maintain oversight over the production of their parts, resulting in greater transparency and accountability. Additionally, we maintain ISO certification and employ the use of FDA/medical-grade materials to ensure our injection molded components fully meet the strict specifications and standards of the medical and pharmaceutical industries.
Plastic injection molding is an efficient and cost-effective method of producing medical and pharmaceutical parts to high levels of precision, accuracy, and quality. It is used to create components from medical devices and equipment to laboratory tools and testing instruments.
How We Can Help
With no minimum order quantities and a free prototype tool with on-demand manufacturing orders, we’re your partner to get to market faster for projects like:
- Lower volume or difficult-to-forecast products
- FDA Class I and II devices, or non-implantable components
- Early-in-development projects
- Components requiring complicated supply chains
- Development stages that require design flexibility
- Parts in which we can apply early process learnings to production
- SKUs that could benefit from a secondary source
- Design verification testing, clinical trial submissions, and regulatory body submission
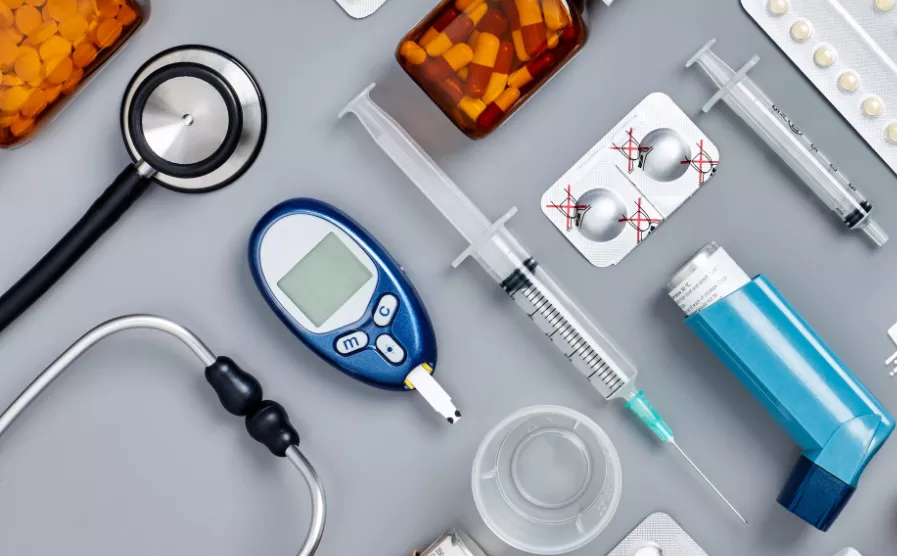
Benefits of Medical Plastic Injection Molding
Rjcmold caters to your need for durable plastic medical components that comply with strict FDA standards and regulations. By employing advanced medical injection molding in our manufacturing process, we are able to supply high volumes of medical components without sacrificing quality while meeting your target specifications.
Our medical plastic injection molding process offers the following benefits:
- Desirable Mechanical Properties: A unique production environment enables the production of medical components bearing desirable mechanical properties, including impact resistance, which protects against wear and tear, and heat resistance, which protects material integrity during repeated sterilization.
- Reduced Risk of Breakage: The production of components under intense pressure reinforces their durability, which increases their resistance to breakage.
- Quality and Regulatory Compliance: Rjcmold uses high-quality, medical-grade materials and employs strict quality control measures to meet strict FDA guidelines on producing products intended for medical use.
- Precision Manufacturing: Mass production of medical components is made possible by the high-volume, precision production capabilities of the medical injection molding process, which enables the production of large quantities of medical products without sacrificing uniformity and quality.
- Cost-Efficient: Due to the process’s ability to process large quantities of high-quality products, the cost of production of all outputs goes down, making it a cost-efficient manufacturing option. In effect, we can pass these savings on to our customers, allowing us to offer competitive prices for our products.
- Broad Material Selection: All-Plastics works with a wide range of medical-grade materials to obtain desired characteristics according to our client’s specifications.
Product Design & Development Support
With our continued investments into engineering resources, our team has the expertise and technical knowledge to assist with your medical device products across various stages and complexity. We love to get involved in the earliest stages of product development to make sure that our customers have the plastic engineering expertise avoiding any costly hiccups in the development process.
We work directly with our customers’ engineering teams, providing guidance on the manufacturability of medical device parts ready to be custom injection molded, or to create a mold design with the proper actions, gate locations, temperature control and venting. Our expertise and experience with medical device injection molding means that we can provide knowledge and assistance that other providers cannot.
By utilizing Sigma Soft mold fill simulation software, we complete a 3D simulation of how the mold fills, packs and cools during the injection molding process as part of our DFM analysis process. Therefore, problems or concerns can be solved before the parts or mold are even produced.
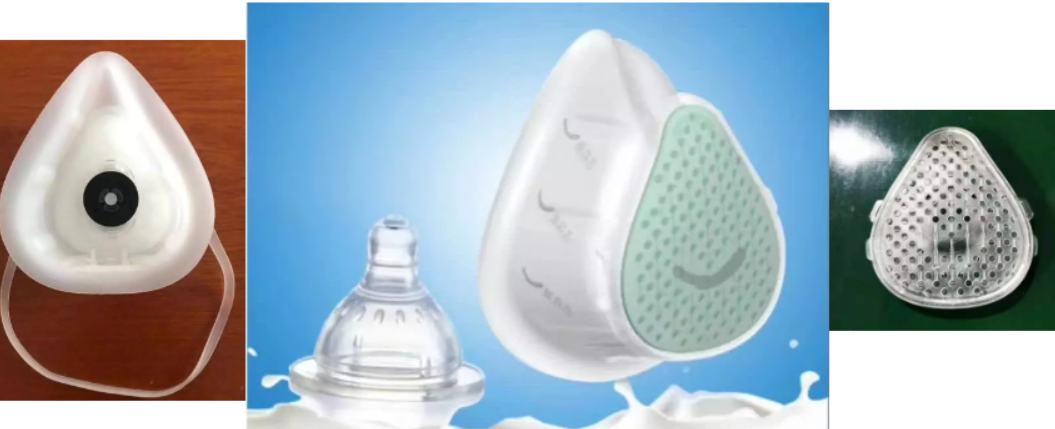
