Stack Molds from RJCmold Thermoplastic Injection Molding and Manufacturing Services
The key to thermoplastic injection molding and manufacturing is efficiency. RJCmold is a leader in the design and construction of complex, precision, multi-cavity molds for the plastic injection molding industry. We provide thin-wall, stack, hot runner, unscrewing and two-shot molds built with the latest methods and technologies available.
Known for their ability to outrace the productivity of single-face molds, stack mold designs from RJCmold. are providing customers from a wide range of industries with high quality custom plastic parts and components at a rapid turnaround. The efficiency derived from stack mold technology comes from using smaller footprint molds that produce multiple parts in smaller molding machines, therefore resulting in lower labor and part costs.
Rjcmold’s unique, molder-friendly approach sets us apart from the competition. We bring you a combination of the best resources available; high technology equipment, quality workmanship, and program management and product development techniques that are flexible enough to meet the needs of one-of-a-kind, multiple cavity and multiple mold programs alike.
Stack Molds
A stack mold can be described as a series of interconnected, same-sized, single-face molds, where the molds are “stacked” next to the other. Thus, without increasing the plastic injection molding machine platen size or tonnage, stack molds double the number of cavities producing parts. Three-level and four-level stack molds triple or quadruple production volumes, respectively.
Stack molds double (or more for increased stack mold levels) the output of standard plastic injection molds, increasing molding efficiency and reducing the overall part cost. Stack molds can also produce multi-component assemblies or a family of parts in one shot on one plastic injection molding machine.
Most stack molds have an equal number of the same cavities in each side of the mold, or parting surface, but they can also have different cavities in each mold parting surface to produce a family of parts per shot, with each part being a different shape and size.
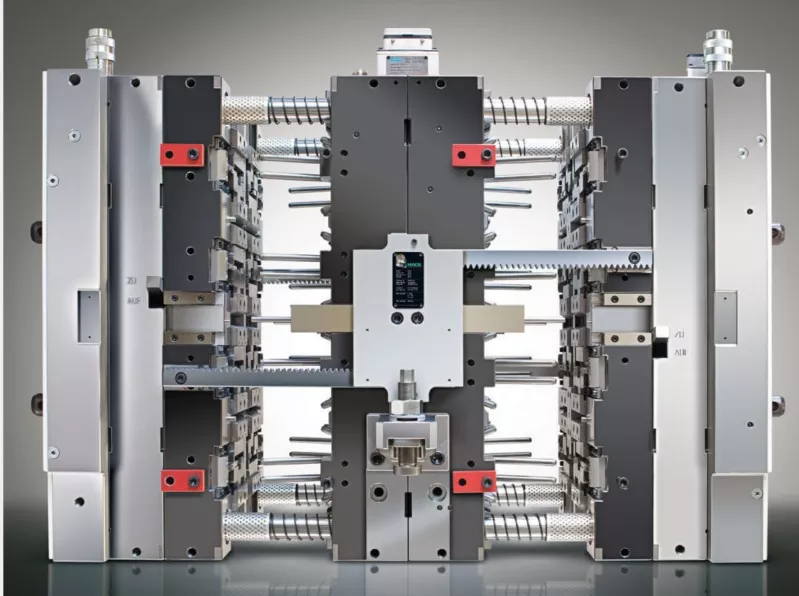
What Is Stack Molding?
Stack molding is really any process that uses multiple mold surfaces to create two or more parts in quick succession. While a traditional single-part mold uses two molding surfaces to create one part, a stack mold might use three molds to create two parts or stack even more to create additional parts in one production cycle. The number of molds depends on the size and complexity of the finished product.
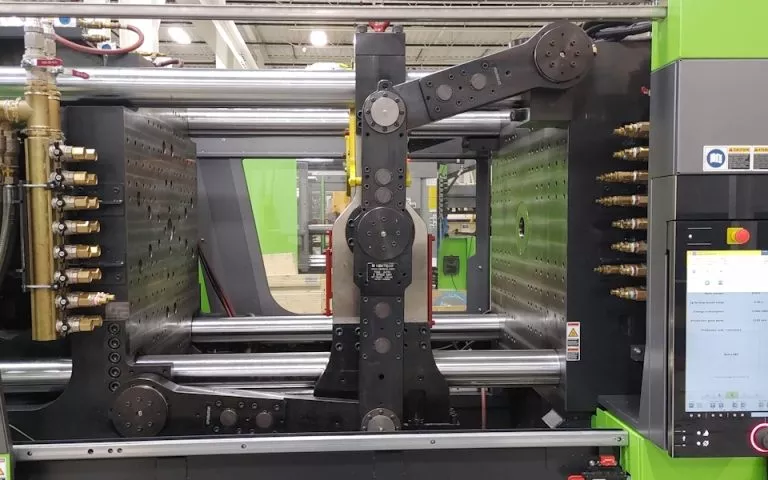
Advantages of Stack Molding
Applications of Rjcmold’s Stack Molds
Stack molds are two single-face molds that are mounted back to back. One half of the core is mounted to the injection-side machine platen while the other half is mounted to the clamp-side machine platen. Cavity plates are fastened to the hot runner system that is located at the center section of the mold. To prevent mold collision, the center section must be equidistant between both core halves at all times. Rjcmold’s stack molds boost productivity, often doubling or quadrupling output. This means less utility and maintenance costs.
Until recently, stack molds were used for fairly small, shallow-draw packaging and other disposable items. Today, innovation has taken hold and a variety of new concepts are broadening the capabilities of stack molds to include larger, multi-material products.
Soft-touch applications such as toothbrush handles, barrier packaging, caps and closures with molded-in liners, multi-color cell phone housings, and combination-material medical parts are in high demand. As knowledge of the benefits of stack molds increases, mold makers and customers alike look to them when applications justify their use.
Put Our Flexibility To Work For You
Stack molding is really any process that uses multiple mold surfaces to create two or more parts in quick succession. While a traditional single-part mold uses two molding surfaces to create one part, a stack mold might use three molds to create two parts or stack even more to create additional parts in one production cycle. The number of molds depends on the size and complexity of the finished product.
Get a Quote Now!
Lower your part cost and gain competitive advantage via Rjcmold experience with stack molds in custom plastic injection molding. Our focus on early supplier involvement in the engineering and design process, design for manufacturability, project management, material selection support and our systems in the United states and China.
Contact Rjcmold to review your current components and assemblies or new development. To learn if stack molds or some of the many other plastic injection molding technologies can provide you a competitive advantage for your application