Two Shot Injection Molding
At RJCMold, we offer high-precision two-shot injection molding services designed to create durable, multi-material, and multi-color parts in a single, efficient process. Our technology seamlessly combines two materials to deliver products that not only look great but also perform exceptionally well in demanding applications.
Request a quote today and bring your designs to life with precision and efficiency. Certified to ISO 9001, ISO 13485, and IATF 16949. Free DFM report & moldflow simulation available.
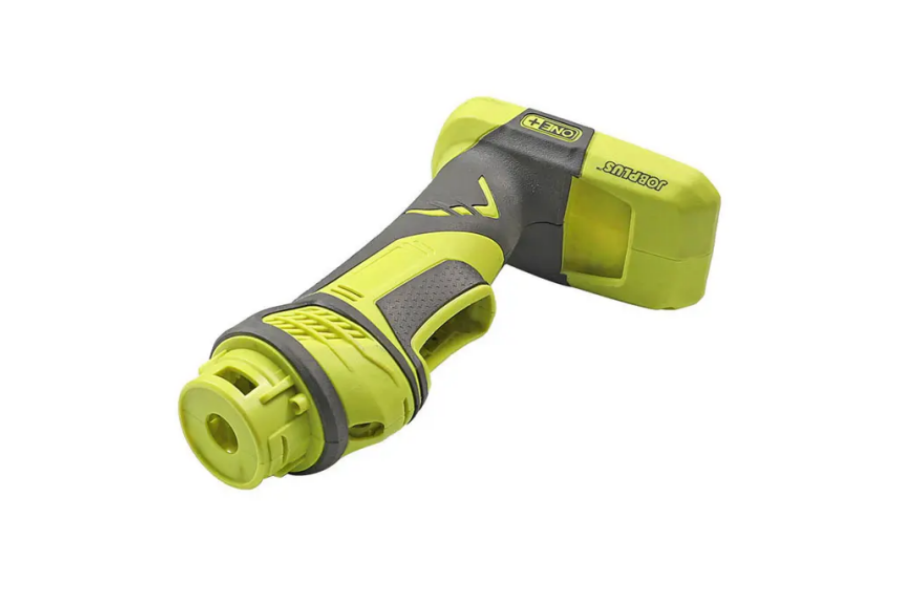
22+
Over 22 Years of Experience in Injection Molding
3000+
Trusted by 3,000+ Enterprise Customers Worldwide
10000+
Completed 10,000+ Custom Injection Molding Projects
20000+
Processed 20,000+ Design Drawings for Manufacturing
What is Two Shot Injection Molding?
Two-shot injection molding (also known as dual-shot or multi-shot molding) is a process in which two different materials or colors are injected into one mold, one after the other, during a single cycle.
By injecting materials in two stages within the same mold, two-shot molding enables the creation of multi-color and multi-material components with precision and durability. Compared to traditional single-color injection molding and secondary assembly, it offers superior aesthetics, better performance, and higher production efficiency.
Advantages of Two Shot Injection Molding
Enhanced Aesthetics
Two-shot molding enables the use of different colors or transparent materials within the same part, eliminating the need for post-processing such as painting or assembly, resulting in visually striking products.
Example: Consumer electronics like smartwatches and wireless earbuds often use two-shot molding to achieve a premium look and feel.
Improved Functionality
The process allows for the combination of soft and hard materials, such as encapsulating a rigid plastic with TPE or TPU, improving grip and comfort.
Example: In medical devices, two-shot molding is used for anti-slip handles and sealing structures, enhancing both usability and safety.
Reduced Production Costs
Traditional multi-material products require additional assembly steps, whereas two-shot molding achieves one-step manufacturing, reducing labor and processing time.
Since the materials bond directly, there is no need for adhesives or welding, leading to further cost savings.
Stronger Product Structure
Two-shot molding creates a durable bond between materials, making the final product more stable and resistant to part loosening or detachment.
Example: In the automotive industry, components like door panels, dashboard buttons, and windshield wiper switches benefit from enhanced durability and quality.
Challenges and Considerations in Two-Shot Molding
Despite its advantages, two-shot molding presents several challenges in production:
Material Compatibility
The key to two-shot molding is ensuring strong adhesion between the two materials. Common material pairings include: PC + ABS, PP + TPE.
Improper material selection may result in delamination or weak bonding.
Complex Mold Design
Two-shot molds are more intricate than single-shot molds and require precise alignment and durability, leading to higher mold costs.
High Equipment Requirements
Two-shot injection molding machines must be equipped with dual injection barrels and rotary or sliding mold functions, demanding high precision and investment.
Strict Process Control
The process requires precise control over temperature, injection pressure, and cooling time to prevent defects such as: Shrinkage, Air bubbles, Weak material bonding.
Application Areas of Two-Shot Injection Molding
Industry | Typical Applications |
---|---|
Consumer Electronics | Smartwatch cases, earbud housings, keyboard keys |
Automotive Manufacturing | Door handles, dashboard buttons, wiper switches |
Medical Devices | Surgical tool handles, anti-slip syringes |
Home Appliances | TV remote controls, kitchen appliance housings |
Daily Necessities | Toothbrush handles, sports bottle caps |
Two Shot Injection Molding vs. Traditional Injection Molding
Feature | Two Shot Injection Molding | Traditional Injection Molding |
---|---|---|
Number of Materials | Two or more | Single material |
Process Efficiency | More efficient for multi-material parts | Requires additional steps for multi-material designs |
Bond Strength | Stronger integration between materials | May require adhesives or mechanical bonding |
Cost | Higher initial cost but lower assembly cost | Lower tooling cost but higher post-processing expenses |
Complexity | Requires specialized equipment | Simpler process |
Overmolding vs. Two-Shot Injection Molding
Overmolding is a broad injection molding process that involves covering a base material with another material (such as plastic or elastomer) to produce a finished part. This process can be completed using either single-mold methods (such as insert molding) or multi-step approaches (such as multi-shot molding).
Two-shot injection molding is a specialized type of Overmolding that involves injecting two different materials into a single mold in two stages. It requires dedicated two-shot injection molding machines and rotary/sliding molds to achieve seamless integration and high-precision parts. While two-shot injection molding falls under the umbrella of Overmolding, the two are not identical: Overmolding is often used for simple encapsulation, whereas two-shot injection molding is ideal for more complex, structurally integrated components.
Comparison | Overmolding | Two-Shot Injection Molding |
---|---|---|
Process Scope | Broad, includes multiple molding methods | Narrow, a specific type of Overmolding |
Mold Type | Single or multi-mold | Single mold with rotary or sliding functions |
Equipment | Standard injection molding machines | Specialized two-shot injection molding machines |
Bonding Method | Mechanical bonding or adhesive | Chemical bonding or mechanical interlocking |
Applications | Simple encapsulation or soft-hard material combinations | High-precision, fully integrated complex parts |