Reaction Injection Molding (RIM)
Reaction Injection Molding (RIM) produces parts with intricate detail that are dimensionally stable, chemically resistant, physically tough, and wear resistant. This is an excellent choice for larger plastic parts produced in short run or low volume production quantities.
What is Reaction Injection Molding (RIM)?
Reaction injection molding (RIM) is a molding process to manufacture plastic molded parts.
The advantage of this process is a low clamping force needed for the mold, long material travel paths and the low pressure conditions of the molding process. The necessary molds can be manufactured quickly and cost effectively using aluminium.
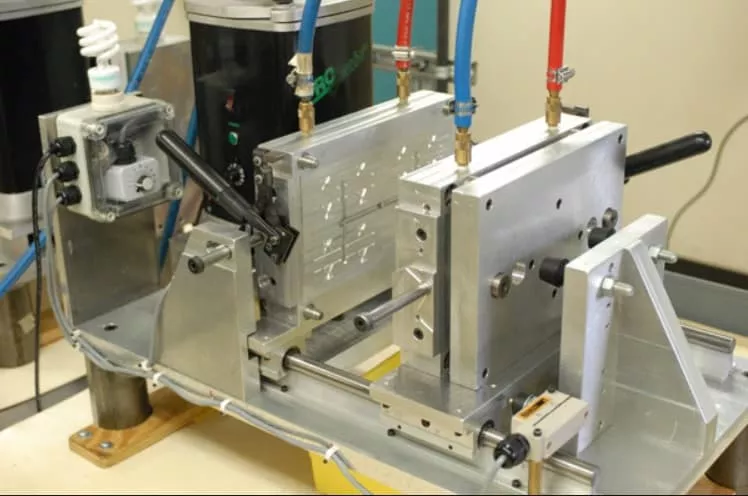
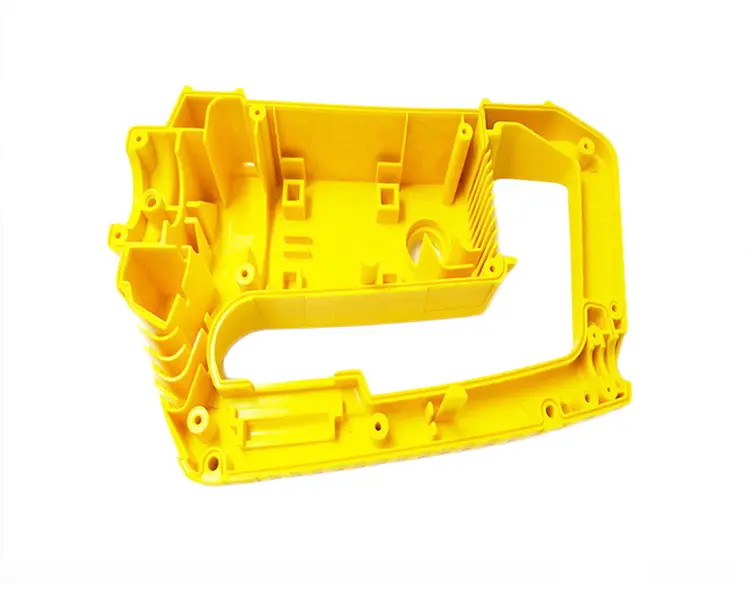
Innovative Solutions for High-class Prototypes and Short Runs
Plastic parts in large series are generally produced by injection molding. The building of the steel mold for this production method is complex and costly and should therefore only be used when a large number of parts warrants its use.
The RIM technology can be used to produce a smaller number of units up to 1,000 parts in a fast and cost-efficient way.
Rjcmold RIM portfolio offers special RIM products with high impact resistance, high temperature resistance, long pot life for production of large parts as well as special certifications for the automotive industry.
Why Reactive Injection Molding?
Reactive injection molding (RIM) is similar to the conventional injection molding (IM) except thermosetting materials are used. The chemical curing reaction occurs simultaneously as the resin flows during the molding process. The polymerization of RIM is usually activated after mixing under heating with or without high pressure. The advantage of RIM is that with its relatively low viscosity, resins can readily fill the cavities with large L/D ratio. The RIM can produce plastic parts with high mechanical strength because of the crosslinking in polymer structures.
However, the thermosetting polymers are usually difficult to be recycled, and the potential problems of flashing, scorching and longer cycle time have been the main challenges of RIM. Moreover, the complicated interplay between chemical reaction, fluid flow and heat transfer bring more uncertainty on process control and optimization for RIM. Rjcmold RIM offers true 3D solutions to analyze RIM processes for thermosetting materials including unsaturated polyester, polyurethane, rubber compound, liquid silicone rubber, and epoxy molding compound. The software simulates cavity filling, curing, part warpage, fiber orientation, multi-component molding, and many other customized methods and processes.
Advantages of Choosing
Reaction Injection Molding
The RIM molding process holds an array of valuable benefits. Here are a few that our customers have found beneficial:
(Due to the liquid injection RIM process and nature of the PUR foaming process, unique, difficult, deep drawn and cylindrical parts can be achieved.)
Materials used in RIM
Resins are generally used: polyurethane resin, vinyl ester, ester-amide resin, unsaturated resin, epoxy resin, traditional composite material, etc.
Commercial materials: HD-PU4210, DCP-RIM, RIM AXSON-875, etc.
PS: The curing time in the RIM process depends mainly on the formulation of molding material and the size of the product. In addition, RIM products need a second cure after the mold removal. Since the RIM process is fast (15-30 minutes / unit) and highly precise, it is suitable for producing large quantities and large products. The size of most casting is 2000mm X 1200mm X 1000mm, for 10KG.
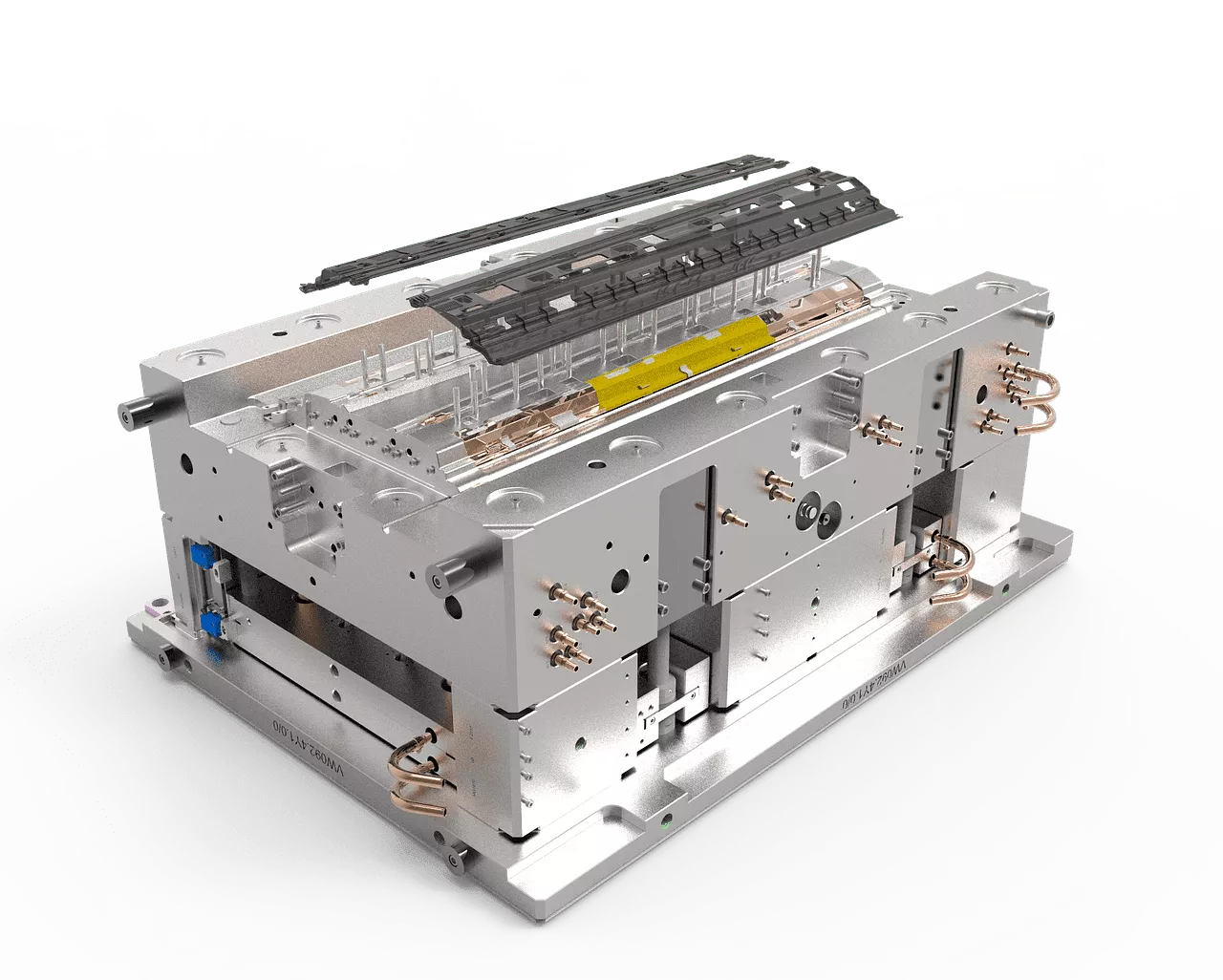
Where can RIM moulding be used?
RIM mouldings can be used across a variety of industries and sectors. From medical to marine, transportation, and everything in-between. These robust mouldings play a crucial role in industries where reliability and durability can be life-saving.
Polyurethane housings are used within the medical and scientific industries to provide parts for innovative cancer treatment, robotic surgery, and laboratory testing equipment. These safety-conscious industries demand compliance against all regulatory standards as well as UL94 V0 flammability ratings and the option for EMC shielding. Electric vehicle charging units, personal dive units, and solar canopies on the other hand require robustness and UV stability so they can stand up to the rigors of external use. RIM mouldings can create precision parts that offer structure and confidence when it counts.
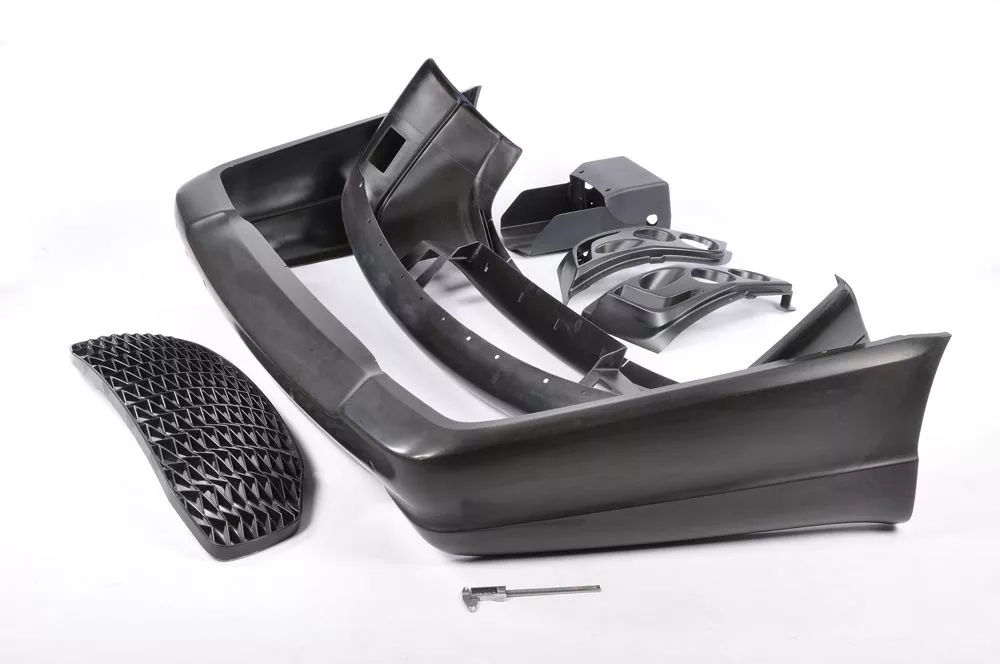
Contact us and receive your personalized Reaction Injection Moulding Quote
Rjcmold is a custom plastic molder specializing in the Reaction Injection Molding (RIM) process. The RIM process allows us to meet our customers’ low-volume injection-molded plastic part needs. We use the RIM process to mold rigid polyurethane plastic parts using low molding pressures and low-mold temperatures. These advantages lead directly to low-cost injection molds, low energy requirements, and low overhead costs.