Fused Deposition Modeling
Fused deposition modeling couples 3D printing’s unparalleled design freedom and fast lead times with production-grade thermoplastics to create durable parts with excellent mechanical properties. This technology is ideal for functional prototypes, durable manufacturing tools, and low-volume end-use parts, and is suitable for aerospace and other industries that rely on certified manufacturing.
Fused Deposition Modeling FDM 3D Printing Service
Fused Deposition Modeling (FDM), also known as Fused Filament Fabrication (FFF), is the most common type of 3D printing. FDM has short lead times, a relatively low cost per part, and can produce larger parts than many other additive polymer technologies. With a variety of material choices and finishing options, our FDM 3D printing service is ideal for creating everything from quick prototypes to the final product.
Benefits of FDM Printing With Us
What is FDM 3D Printing?
Fused Deposition Modeling (FDM) is a 3D printing technology widely known for its speed, accuracy, and competitive cost. An FDM machine precisely extrudes melted plastic filament to create a part. FDM parts can be made in as fast as one day.
Fused Deposition Modeling 3D printing service offers large build volumes up to 24″ x 36″ x 36″ platforms. FDM offers the largest variety of colors and selection of production-grade thermoplastics of any 3D printing process. Material range from general-purpose ABS or ASA to high performing polycarbonate and heat resistant ULTEM.
How Fused Deposition Modeling Works
Fused Deposition Modeling (FDM), also known as Fused Filament Fabrication (FFF), is the most well-known form of 3D printing that involves melting, extruding, and depositing thermoplastic filament onto a print bed to build objects layer-by-layer. A popular choice for rapid prototyping, FDM can be used to create custom manufacturing aids and small production parts. FDM also allows the printing of larger objects.
FDM offers the largest variety of production-grade thermoplastics and colors of any 3D printing process. We offer prevailing engineering-grade FDM filament materials including PLA+, ABS, ASA, PETG, PC, and TPU along with premium engineering-grade FDM materials exhibiting outstanding strength and thermal stability for advanced tooling and prototyping applications in the automotive, aerospace, and medical industries, such as PEEK and ULTEM®.
Support structures are necessary when for constructing complex geometries with FDM, which means prints will require additional material, time, and post-processing.
FDM Technical specifications
Specifications | |
---|---|
Maximum Part Size: | 24 x 36 x 36 inches (610 x 914 x 914 mm) |
Minimum Wall Thickness: | 0.1 inches (2.5 mm) |
Minimum Feature Size: | 0.016 inches (0.4 mm) |
Best Achievable Tolerance: | +/- 0.0035 inches or +/- 0.0015 inches per inch (+/- 0.089 mm or +/- 0.0015 mm per mm) depending on geometry |
Lead Time: | Can be as low as 3 days |
Materials: |
|
General Tolerances for FDM 3D Printing
Tolerance Note | Description |
---|---|
General Tolerance |
|
Build Size | Up to 24″ x 36″ x 36″ |
Layer Height, less than 16″ | 0.010″ Layers (0.008″ for PLA) |
Layer Height, greater than 16″ (up to 36″) | 0.013″ Layers |
Minimum Wall Thickness | 0.047″(less than 16″), 0.060″ (greater than 16″) |
FDM 3D printed parts can be built up to 24″ x 36″ x 36″. Stratasys Fortus 400/450-series machines will produce parts up to 16″ and Stratasys Fortus 900MC or F900 platforms are used for parts larger than 16″. Prototyping PLA is built on Prusa MK3S desktop FFF machines with a build volume of 9.8″ x 8.3″ x 8.3. General tolerances apply before secondary finishing or post-processing unless otherwise specified. To learn more tips about FDM 3D printing check out our Fused Deposition Modeling (FDM) Design Guide.
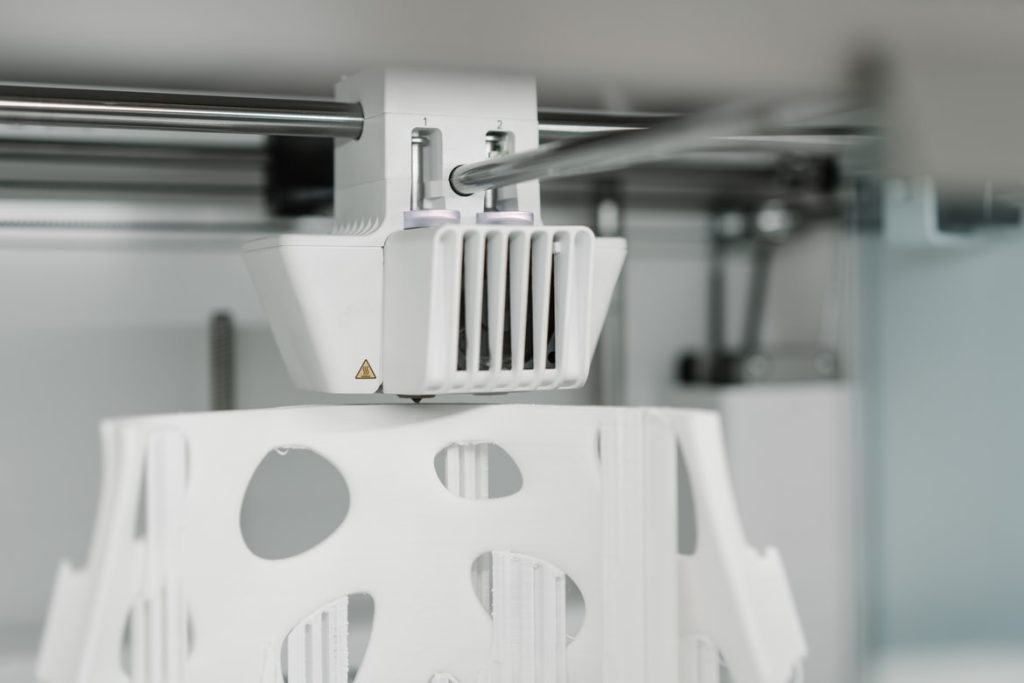
Prototyping PLA
Why Choose FDM?
FDM uses many of the same materials used in injection molding. FDM parts can be used to test a design before transitioning to the production process. This allows designers and engineers to identify any issues and make improvements early in the design process. The ability to test early saves a lot of time and money in the long run. A functional prototype can be produced within a few hours or days, depending on the complexity of the part. Having a functional prototype reduces the time to market and helps maximize overall product performance.
FDM technology also presents an opportunity to create custom tooling and fixtures. This allows a customer the flexibility to take on new projects while lowering costs and risks in a timely manner — much quicker than traditional production. Injection molding is an extremely cost effect manufacturing process but the up front cost for mold tooling can be cost prohibitive when running only a few parts for testing. Printing with FDM will allow engineers the ability to create and test a part without the cost and time associated with injection mold making.
A low-volume production run is easy with FDM. There is no minimum quantity requirement; make as much or as little as is required. Production can start as soon as a Computer-Aided Design (CAD) design file is available and translated to the 3D printing machine.
Get a FDM 3D Printing Quote from RJCmold
FDM is a fast and cost-effective 3D printing process whereby plastic resin is deposited layer-by-layer, producing a functional and durable part great for concept modeling or low-volume production.Quickly get a quote in as soon as one hour on any FDM 3D printing project today with our instant quote platform.