Die Casting Mould Service
If you have a project that requires plastic and metal parts service, you’ve come to the right place! RJC is a premier mold making services company specializing in high quality parts, plastic mold/molding parts and die casting molds and components at affordable prices for a wide range of industries including lighting, medical, automotive, electrical, and more. Molds and formed parts, including all finishing steps, surfaces and assembly. With many years of experience, we are able to produce custom die-cast molding parts according to customers’ specifications, drawings or samples. We have advanced technology, highly skilled staff, high quality moulds and high pressure die casting process to ensure mould parts are of the highest quality and cost-effectiveness.
Advantages of Our Die Casting Mould Manufacturing Services
- We have more than 20 years of rich experience in manufacturing die casting mold parts and have won a good reputation.
- Our engineers can combine a variety of processes and use their extensive experience to reduce costs, so the price of our die casting mold products is cost-effective.
- Complete parts on time to provide the best support for your R&D projects.
- Excellent customer service and communication.
- Precision die-cast molding parts manufacturing according to your drawings or samples.
- High production capacity and competitive price.
- On time delivery.
Powerful technical team provide you best die casting solution
- Based on experience, we will give you appropriate suggestions for product structure and thickness, assist you to amend drawings and die casting blank drawings, then offer detailed DFM analysis for your confirmation.
- RJCmold’s engineering team can make mold flow analysis, and design the most appropriate runner system and mould structure combineing the result of mold flow analysis, to ensure high quality of die casting mould and product.
- Organize appraisal meetings, related engineers and technical directors will make comprehensive feasibility assessments of product design, DFM analysis, mould flow analysis, mould structure, mould manufacture, die casting production, product CNC machining, surface treatment, packing and delivery. Finally we’ll feed back the meeting results to our clients.
When looking for fast large-scale production of parts without sacrificing detail and surface quality, die casting is a perfect manufacturing option.
RJC offers extensive experience in helping our clients select the right process or combination of processes to meet their project goals. RJC has developed a very advanced manufacturing system that shortens the production cycle to the extreme. Our experience and systems are able to quickly converge on a solution, reduce process variability, and deliver iteratively to very compressed timelines.
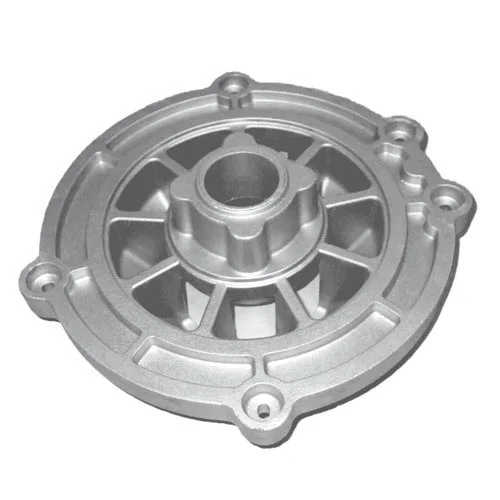
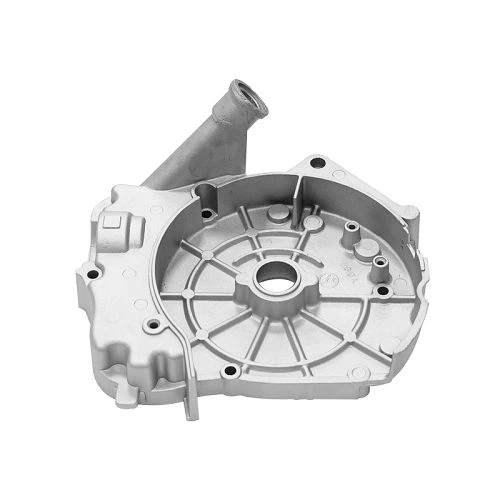
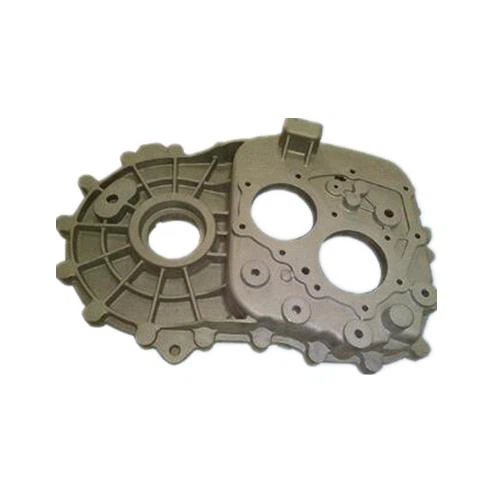
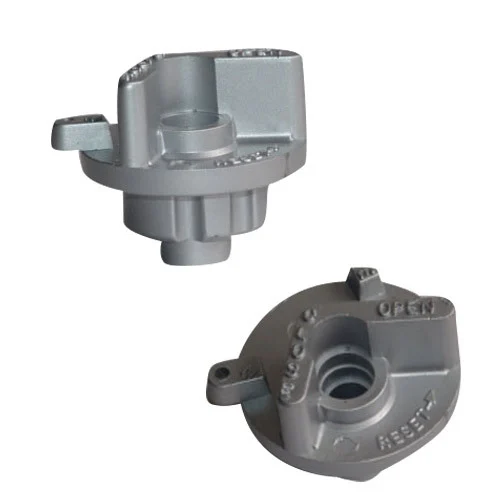
Die Casting Mould
Die-casting mold is a technology for mass production of metal products and components, and die-casting mold is one of the three major elements of die-casting production. This is a process done on a special die-casting die forging machine. The basic process flow is: liquid metal is first filled into the cavity of the mold by low-speed or high-speed casting, and the mold has a movable cavity surface. It is forged under pressure along with the cooling process of the molten metal, which not only eliminates the shrinkage and porosity defects of the blank, but also makes the internal structure of the blank reach broken grains in the forging state. The comprehensive mechanical properties of the blanks are significantly improved.
Die-casting molds basically consist of two parts, consisting of fixed (fixed) and movable (ejection) mold halves. The fixed mold half is installed on the fixed fixed plate of the die casting machine; the top mold half is fixed on the movable fixed plate and includes a casting ejector. When ready to cast, the two mold halves are closed and held closed by the clamping force on the machine. The contact surface between the two mold halves is called the mold parting surface or the mold parting surface. The opening and closing motion is only for ejector. Cavities or undercuts are demolded by mechanically or hydraulically operated core slides (cores).
Die Casting Mould Design Process
Designing a mold involves processes that come with multiple categories.
- Preparation Phase: This is the phase where the validity of the product is evaluated from a dimensional and geometrical standpoint.
- Cavity Numbers: Cavity orientation, product count, and hypothetical time cycle have to be considered for the cavity mold’s best option.
- Projection Place: Projection has a significant role in the designing phase. It is also where the surface is created from the cavities plan.
- Die Volume & Shape: Volume and shape are essential in mold design. Here, the cavities’ sizes can be molded accurately.
- Simulation: This helps calculate the mold filling method. The modality depends on the filling process and process of the cast piece.
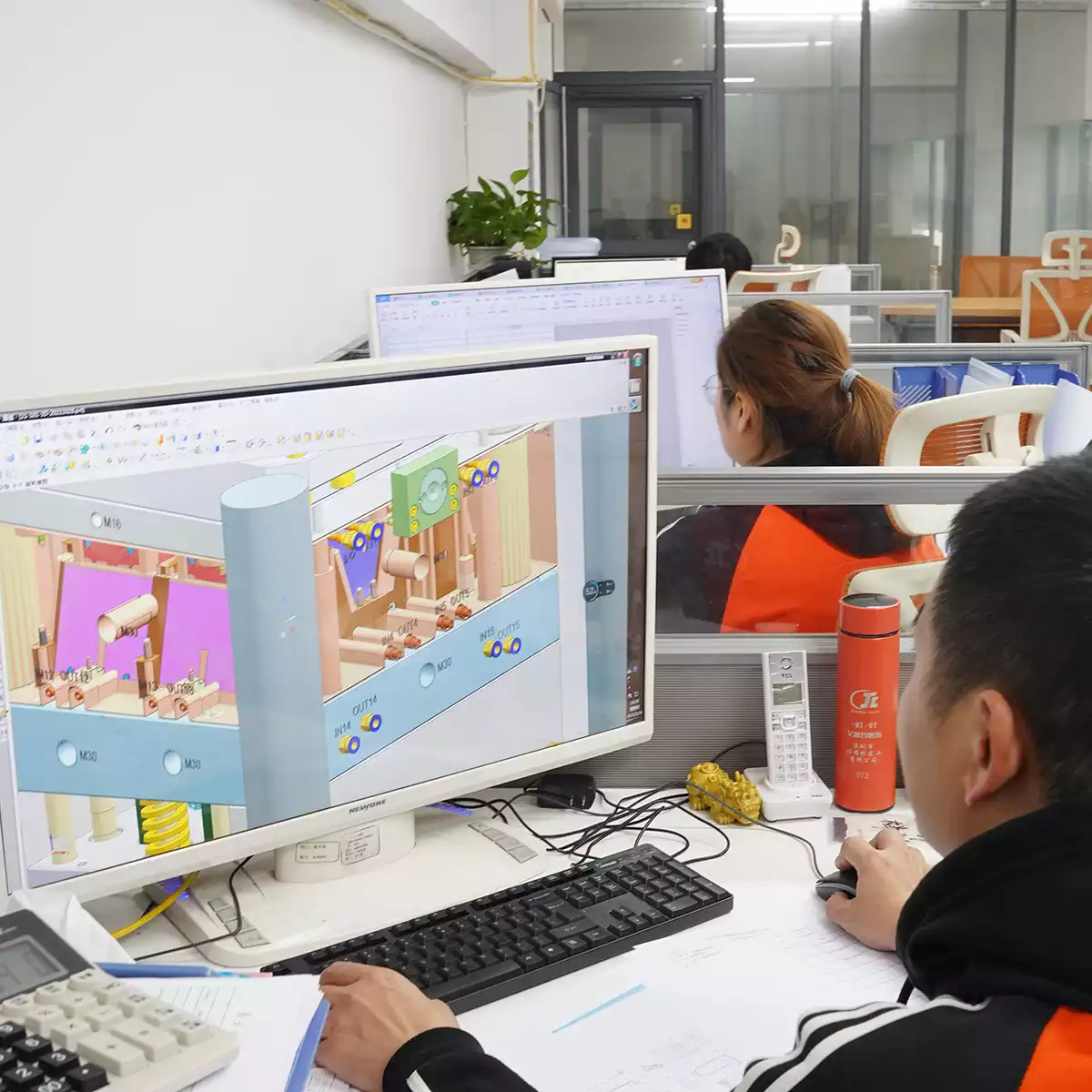
Affordable Tooling Services
Price is a challenge in die casting, particularly for tooling. RJCmold has gone to great lengths to make our services affordable for smaller manufacturers. We are proud to offer tooling around 10% of the cost of our competitors. In addition, we offer piece part prices 10-20% below the competition.
How are Die Castings Made?
Steel dies capable of producing tens of thousands of castings in quick succession must be made in at least two sections to allow the castings to be removed. These parts are firmly mounted in the machine and are arranged so that one is stationary (fixed die half) and the other one is movable (syringe half-mold). To begin the casting cycle, the two mold halves are clamped together by a die-casting machine. Molten metal is injected into the mold cavity and rapidly solidified. The mold half is opened and the casting is ejected. Die-casting molds can be simple or complicated, with moveable slides, cores or other parts, depending on the complexity of the casting.
To date, the complete cycle of die casting has been the fastest cycle to produce precision nonferrous metal parts. This is in stark contrast to sand casting, which requires new sand molds for each casting. Although the permanent mold process uses iron or steel molds instead of sand, it is much slower and less precise than die castings.
Watch the video of our die casting facility to learn how die castings such as aluminum die castings, zinc die castings are made. Video also available on youtube.com.
Die casting mold material
RJC provides aluminum, zinc alloy and steel, stainless steel die casting molds: 4140, 4130, A36, 1018, 303, 304, 410, 17-4, 2205 Duplex, 440C, 420, 316, 904L, 2024, 5083, 6061 , 6063, 7050, 7075 etc.
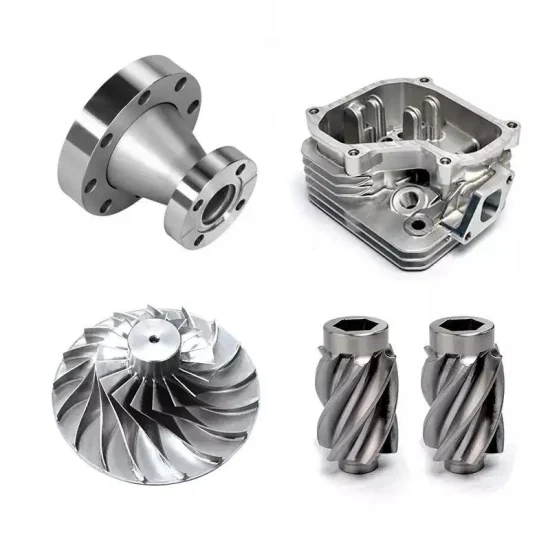
Mold production service
Our die casting mold production facilities include our own CNC machining centers, lathes and milling machines, spark erosion machines and polishing systems.
The following equipment can be used to make die casting molds:
- CNC Milling Center
- Lathes and Mills
- Spark Erosion (EDM) Machines
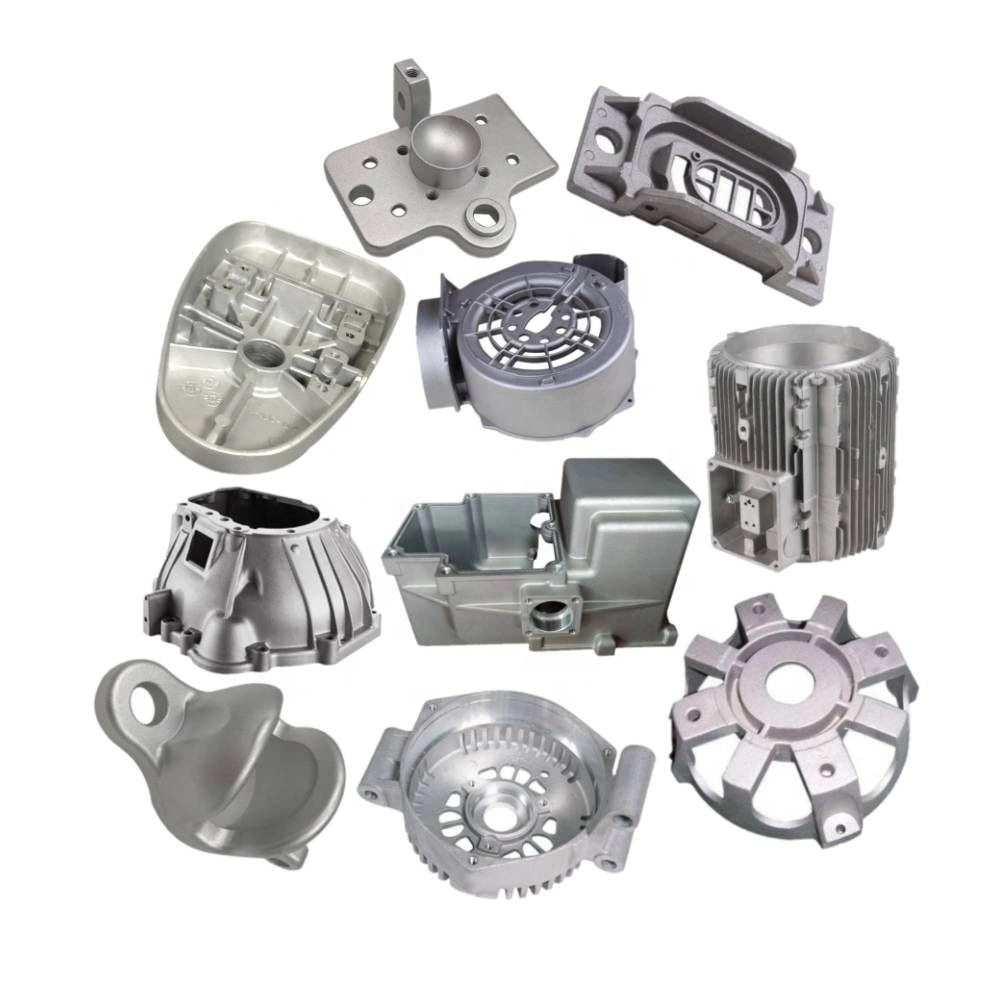
Contact RJCmold for Custom Die Casting Services Today
Contact us for more information at mold@rjcmold.com regarding our custom die casting processes and applications, or request a quote
for an in-depth price analysis today. At RJCmold, we provide you with advanced die casting solutions for your specific metal die casting application needs.