In the contemporary landscape of product development, the ability to swiftly transform conceptual designs into tangible prototypes has emerged as a pivotal factor in determining the success of businesses across diverse industries. Rapid prototyping, a revolutionary approach, has disrupted traditional manufacturing processes by enabling the expedited creation of physical models with a high degree of precision and flexibility. This article aims to embark on an in-depth journey into the world of rapid prototyping, dissecting its multifaceted techniques, exploring its extensive applications, weighing its significant benefits against potential challenges, and ultimately providing a comprehensive understanding of its role in modern product development. Whether you are a seasoned professional in the fields of engineering and design or an aspiring entrepreneur with a groundbreaking idea, a thorough comprehension of rapid prototyping can equip you with the necessary tools to navigate the complexities of bringing your vision to fruition.
What is Rapid Prototyping?
Rapid prototyping, at its core, encompasses a set of automated manufacturing processes that facilitate the creation of a physical prototype of a product or component within a relatively short timeframe. This process typically commences with a digital model generated using computer-aided design (CAD) software. The CAD data serves as the blueprint, guiding the subsequent manufacturing operations, which may include 3D printing, computer numerical control (CNC) machining, or injection molding. The primary objective of rapid prototyping is to produce a functional or aesthetic representation of the final product, enabling designers and engineers to evaluate its form, fit, and functionality at an early stage of the development cycle.
One of the most compelling advantages of rapid prototyping is its iterative nature. Unlike traditional manufacturing methods that often involve significant time and cost investments in tooling and setup, rapid prototyping allows for the quick production of multiple prototypes. This iterative process empowers designers to test various design concepts, incorporate feedback, and make necessary refinements in a timely manner. By identifying and addressing potential issues early on, rapid prototyping helps to minimize the risk of costly errors and delays that could occur during the later stages of mass production.
Rapid Prototyping Techniques
3D Printing
3D printing, also known as additive manufacturing, has emerged as one of the most popular and widely adopted rapid prototyping techniques in recent years. This innovative process involves the sequential deposition of material in layers to build a three-dimensional object from a digital model. There are several distinct 3D printing technologies available, each with its own unique characteristics and applications.
Fused Deposition Modeling (FDM) is perhaps the most accessible and commonly used 3D printing technology. It operates by melting a thermoplastic filament, such as polylactic acid (PLA) or acrylonitrile butadiene styrene (ABS), and extruding it through a heated nozzle. The nozzle deposits the molten material layer by layer, following the instructions encoded in the CAD file. FDM is renowned for its affordability, ease of use, and relatively large build volumes, making it an ideal choice for hobbyists, small businesses, and educational institutions. However, it may have limitations in terms of precision and surface finish compared to other 3D printing technologies.
Stereolithography (SLA) is a more advanced 3D printing technique that utilizes a laser to cure a liquid resin. The laser selectively hardens the resin layer by layer, creating a solid object. SLA offers exceptional precision and surface finish, making it suitable for producing highly detailed and complex prototypes. It is commonly used in industries such as jewelry, dentistry, and automotive design, where intricate geometries and fine details are required. However, SLA is relatively more expensive than FDM and requires additional post-processing steps to remove support structures and finish the surface.
Selective Laser Sintering (SLS) is a powder-based 3D printing technology that uses a laser to sinter powdered materials, such as nylon or metal, together. The laser selectively fuses the powder particles, layer by layer, to form a solid object. SLS is capable of producing strong and durable prototypes with excellent mechanical properties. It is often employed in applications where high strength and resistance to wear and tear are essential, such as aerospace and automotive components. However, SLS machines are typically more expensive and require specialized handling and maintenance.
Digital Light Processing (DLP) is another 3D printing technology that uses a digital projector to cure a liquid resin. The projector projects a series of images onto the resin surface, causing it to harden layer by layer. DLP offers high speed and precision, making it suitable for producing large quantities of prototypes in a relatively short time. It is commonly used in industries such as consumer goods, medical devices, and entertainment, where rapid turnaround times and high-quality prototypes are crucial.
3D Printing Technology | Precision (mm) | Build Volume | Material Options | Cost |
---|---|---|---|---|
FDM | 0.1 – 0.5 | Small to Medium | Thermoplastics (PLA, ABS, Nylon, etc.) | Low |
SLA | 0.05 – 0.1 | Small to Medium | Photopolymer Resins | Medium |
SLS | 0.1 – 0.2 | Medium to Large | Nylon, Polyamide, Metal Powders (e.g., Stainless Steel, Titanium) | High |
DLP | 0.05 – 0.1 | Small to Medium | Photopolymer Resins | Medium |
CNC Machining
CNC machining is a subtractive manufacturing process that involves the use of computer-controlled cutting tools to remove material from a workpiece. It is a highly versatile and precise method for creating prototypes and production parts. CNC machines can be programmed to perform a wide range of operations, such as milling, turning, drilling, and tapping, allowing for the creation of complex geometries with high accuracy.
Milling machines are the most commonly used CNC machines for rapid prototyping. They utilize a rotating cutting tool to remove material from the workpiece, creating the desired shape. Milling machines can be equipped with various types of cutting tools, such as end mills, ball nose mills, and face mills, depending on the specific requirements of the project. Lathes, on the other hand, are used to machine cylindrical parts by rotating the workpiece and using a cutting tool to remove material. Routers are typically used for cutting flat materials, such as wood, plastic, or composites.
CNC machining offers several advantages over other rapid prototyping techniques. It can achieve high levels of precision and repeatability, making it suitable for producing parts with tight tolerances. It also allows for the machining of a wide range of materials, including metals, plastics, and composites. Additionally, CNC machining can produce parts with excellent surface finish and mechanical properties. However, CNC machining is generally more expensive and time-consuming than 3D printing, especially for small batch production or complex geometries.
CNC Machine Type | Precision (mm) | Material Options | Cost |
---|---|---|---|
Milling Machine | 0.01 – 0.1 | Metals (Aluminum, Steel, Titanium), Plastics (ABS, Polycarbonate), Composites (Carbon Fiber, Fiberglass) | Medium to High |
Lathe | 0.01 – 0.1 | Metals (Aluminum, Steel, Brass), Plastics (Nylon, Delrin) | Medium to High |
Router | 0.1 – 0.5 | Wood, Plastic, Composites (Plywood, MDF, Acrylic) | Low to Medium |
Injection Molding
Injection molding is a manufacturing process that involves injecting molten material into a mold cavity to create a solid object. It is a widely used method for mass production of plastic parts, but it can also be employed for rapid prototyping, although with some limitations. Injection molding requires the creation of a mold, which is typically made of metal and is designed to replicate the shape of the final product.
The injection molding process begins with the heating of the plastic material until it reaches a molten state. The molten plastic is then injected into the mold cavity under high pressure. Once the plastic has cooled and solidified, the mold is opened, and the finished part is ejected. Injection molding offers several advantages, such as high production rates, excellent surface finish, and the ability to produce complex geometries with consistent quality. However, it is a relatively expensive and time-consuming process, especially for small batch production or rapid prototyping. The cost of tooling and setup for injection molding can be significant, and it may not be economically viable for producing a small number of prototypes.
Injection Molding Parameter | Value |
---|---|
Precision (mm) | 0.01 – 0.1 |
Material Options | Thermoplastics (Polyethylene, Polypropylene, Polystyrene), Thermosetting Plastics (Epoxy, Phenolic) |
Cost (for prototype) | High |
Production Volume | High |
Applications of Rapid Prototyping
Product Design and Development
Rapid prototyping has revolutionized the field of product design and development by enabling designers to quickly and easily test and validate their concepts. By creating physical prototypes, designers can gain a better understanding of the product’s form, fit, and functionality, and make informed decisions about its design. Rapid prototyping also allows designers to communicate their ideas more effectively to stakeholders, such as clients, investors, and manufacturers, by providing a tangible representation of the product.
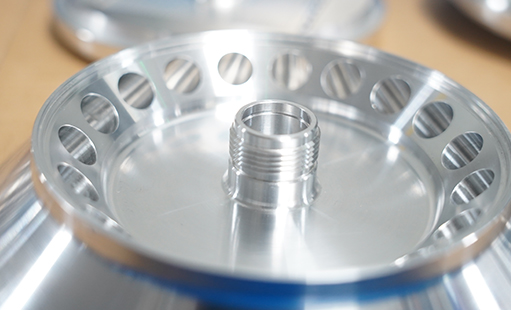
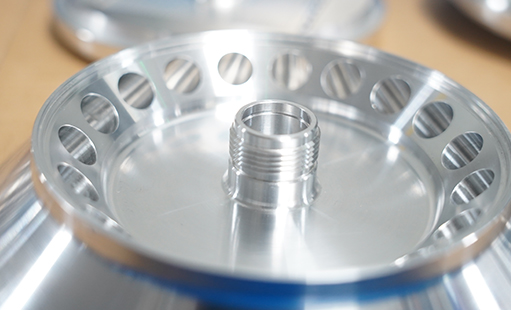
For example, consider the design of a new smartphone. Using rapid prototyping, designers can create a series of prototypes to test different aspects of the phone’s design, such as its ergonomics, user interface, and camera placement. By gathering feedback from users and stakeholders, designers can make iterative improvements to the design, ensuring that the final product meets the needs and expectations of the market.
Medical Device Development
The medical device industry is highly regulated and requires rigorous testing and validation of new products before they can be approved for use. Rapid prototyping plays a crucial role in the development of medical devices by allowing manufacturers to quickly create prototypes for testing and evaluation. By using rapid prototyping techniques, medical device manufacturers can reduce the time and cost associated with the development process, while also improving the quality and safety of their products.
For instance, in the development of a new implantable medical device, such as a pacemaker or a hip implant, rapid prototyping can be used to create a prototype of the device for testing its compatibility with the human body, its functionality, and its durability. By conducting thorough testing on the prototype, manufacturers can identify and address any potential issues before investing in the production of the final device.
Aerospace and Defense
The aerospace and defense industries demand high-performance components that can withstand extreme conditions and meet strict safety and reliability standards. Rapid prototyping is widely used in these industries to develop and test new components, such as engine parts, structural components, and avionics systems. By using rapid prototyping techniques, aerospace and defense companies can reduce the development time and cost of new products, while also improving their performance and reliability.
For example, in the development of a new aircraft engine, rapid prototyping can be used to create prototypes of the engine components, such as the turbine blades and the combustion chamber. By testing these prototypes under simulated flight conditions, engineers can optimize the design of the engine components, ensuring that they meet the required performance and safety standards.
Automotive Industry
The automotive industry is constantly evolving, with new technologies and designs emerging every year. Rapid prototyping is an essential tool in the automotive industry for developing and testing new vehicle components, such as engines, transmissions, and body parts. By using rapid prototyping techniques, automotive manufacturers can reduce the development time and cost of new vehicles, while also improving their performance, fuel efficiency, and safety.
For instance, in the development of a new electric vehicle, rapid prototyping can be used to create prototypes of the battery pack, the electric motor, and the charging system. By testing these prototypes in real-world conditions, engineers can optimize the design of the vehicle components, ensuring that they meet the required performance and safety standards.
Benefits of Rapid Prototyping
Faster Time to Market
One of the most significant benefits of rapid prototyping is its ability to accelerate the product development process. By enabling the quick production of prototypes, rapid prototyping allows designers and engineers to test and validate their designs in a shorter timeframe. This iterative process helps to identify and address potential issues early on, reducing the risk of delays and costly rework during the later stages of development. As a result, products can be brought to market faster, giving companies a competitive edge in the marketplace.
Cost Savings
Rapid prototyping can also lead to significant cost savings in the product development process. By creating prototypes early in the development cycle, designers and engineers can identify and address potential issues before investing in expensive tooling and production equipment. This helps to reduce the risk of costly mistakes and rework, which can significantly increase the overall cost of the project. Additionally, rapid prototyping allows for the production of small batches of prototypes, which can be used for testing and evaluation without the need for large-scale production runs. This further reduces the cost of the development process, especially for products with uncertain market demand.
Improved Design Quality
Rapid prototyping provides designers and engineers with the opportunity to test and evaluate their designs in a physical form, which can help to improve the overall quality of the design. By creating multiple prototypes and testing them under different conditions, designers can identify potential issues and make necessary refinements to the design. This iterative process helps to ensure that the final product meets the required specifications and performance criteria, while also improving its usability, functionality, and aesthetics.
Enhanced Communication
Rapid prototyping can also enhance communication and collaboration between designers, engineers, and other stakeholders involved in the product development process. By providing a tangible representation of the product, rapid prototyping makes it easier for stakeholders to visualize and understand the design concept. This can help to facilitate better communication and collaboration, as stakeholders can provide feedback and suggestions based on their own observations and experiences. Additionally, rapid prototyping allows for the quick and easy production of multiple prototypes, which can be used for testing and evaluation by different stakeholders. This helps to ensure that all stakeholders have the opportunity to provide input and feedback on the design, leading to a more comprehensive and well-rounded product.
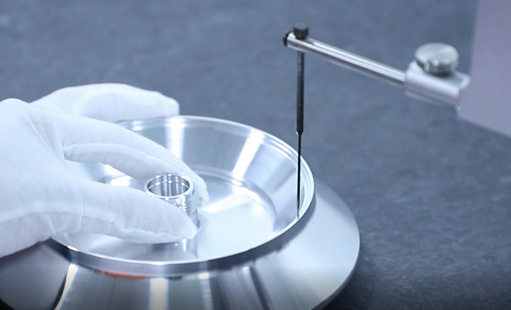
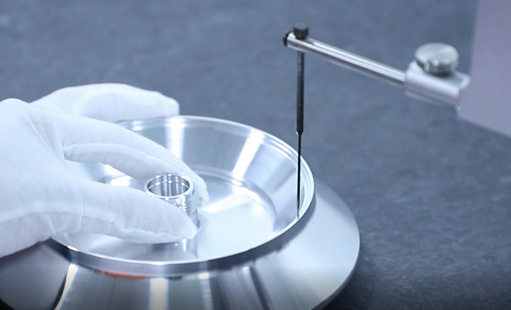
Challenges of Rapid Prototyping
Limited Material Options
One of the primary challenges of rapid prototyping is the limited range of materials available. While there has been significant progress in the development of new materials for rapid prototyping, the available options are still relatively limited compared to traditional manufacturing methods. This can be a significant limitation, especially for applications that require specific material properties, such as high strength, durability, or heat resistance.
High Cost
Rapid prototyping can be a relatively expensive process, especially for complex or large-scale prototypes. The cost of materials, equipment, and labor can add up quickly, making it difficult for some companies to justify the investment. Additionally, the cost of tooling and setup for certain rapid prototyping techniques, such as injection molding, can be significant, especially for small batch production or rapid prototyping.
Limited Precision
While rapid prototyping techniques have made significant advancements in terms of precision and accuracy, they still have limitations compared to traditional manufacturing methods. Some rapid prototyping techniques, such as 3D printing, may not be able to achieve the same level of precision and accuracy as CNC machining or injection molding. This can be a significant limitation, especially for applications that require tight tolerances and high levels of precision.
Post-Processing Requirements
Most rapid prototyping techniques require some degree of post-processing to finish the surface of the prototype and remove any support structures. This can add time and cost to the prototyping process, especially for complex prototypes. Additionally, post-processing can be a challenging and time-consuming task, requiring specialized skills and equipment.
Frequently Asked Questions (FAQs)
-
What distinguishes rapid prototyping from traditional prototyping methods in terms of their underlying principles?
Rapid prototyping fundamentally diverges from traditional prototyping methods in its reliance on automated manufacturing processes driven by digital data. Traditional prototyping often entails manual craftsmanship, such as hand carving or casting, which is labor-intensive and time-consuming. In contrast, rapid prototyping leverages technologies like 3D printing, CNC machining, and injection molding, which are controlled by computer programs. This automation enables the swift production of prototypes with a high degree of precision and consistency, facilitating rapid iteration and design refinement. -
Could you elaborate on the factors that should be considered when choosing a material for rapid prototyping?
When selecting a material for rapid prototyping, several crucial factors come into play. Firstly, the intended application of the prototype is of utmost importance. For example, if the prototype needs to withstand high temperatures or mechanical stress, materials with appropriate thermal and mechanical properties, such as metals or high-performance plastics, should be considered. Secondly, the properties of the material, such as its strength, durability, and chemical resistance, must align with the requirements of the application. Additionally, the cost of the material, its availability, and the compatibility with the chosen rapid prototyping technique are also significant considerations. For instance, some materials may be more suitable for certain 3D printing technologies than others. -
How does the choice of rapid prototyping technique impact the time required to create a prototype?
The time required to create a prototype varies significantly depending on the chosen rapid prototyping technique. 3D printing, particularly technologies like FDM, can often produce prototypes relatively quickly, especially for small and simple designs. However, more complex geometries or larger build volumes may require longer printing times. SLA and DLP, which are based on curing liquid resins, can also be relatively fast for certain applications but may require additional post-processing time. CNC machining, on the other hand, is generally more time-consuming, especially for intricate designs, as it involves the sequential removal of material from the workpiece. Injection molding, while highly efficient for mass production, requires a significant amount of time for mold design, fabrication, and setup, making it less suitable for rapid prototyping of small quantities. -
What are the potential cost-saving strategies that can be employed when utilizing rapid prototyping services?
There are several cost-saving strategies that can be implemented when using rapid prototyping services. Firstly, optimizing the design of the prototype can help reduce material usage and machining time. By simplifying the geometry and eliminating unnecessary features, the cost of materials and the time required for production can be minimized. Secondly, choosing the appropriate rapid prototyping technique based on the specific requirements of the project can also lead to cost savings. For example, if a prototype does not require high precision or complex geometries, a more cost-effective technique like FDM may be sufficient. Additionally, working with a reputable rapid prototyping service provider that offers competitive pricing and value-added services, such as design optimization and material selection guidance, can help ensure that the project is completed within budget. -
In what ways can rapid prototyping contribute to the sustainability of product development processes?
Rapid prototyping can contribute to the sustainability of product development processes in several ways. Firstly, by enabling rapid iteration and design refinement, it helps to reduce the number of design flaws and errors, which can lead to fewer product recalls and waste. Secondly, the ability to produce small batches of prototypes allows for more efficient use of materials, as there is less need for large