Plastic Injection Mold Maker
RJCmold is A plastic injection mold maker with over 20 years of experience. We offer a complete manufacturing solution that covers every aspect of raw material verification, tool making, part fabrication, finishing, and final inspection.
Our team of manufacturing experts is committed to providing you with support for plastic injection mold of any size or complexity.
Design to actualization services. From beginning to end, you can trust RJCmold’s experienced hands to bring your vision to life.
Our Core Business Services
we provide many Precision plastic injection mold &tooling solutions,
Plastic injection molding solutions and Silicone rubber part solutions; anyway, please contact us for your product service.
WHY WORK WITH US
One-stop Solution Expert
We Are Ready To Help Find Your Ideal Solution
- Come to us with your concept, sketch, CAD or 3D parts drawing. We will design and develop your idea into a workable product.
- Before molds, we would make prototypes for you to check the design and assembly.
- Expert manufacturability analysis.
Commonly known as DFM and moldflow analysis, our team of engineers perform expert manufacturability analysis on your injection molded parts at no charge. As a result, we have netted savings to you of up to 50% reduction in manufacturing costs! - 10+ years of experience, help you select and evaluate suitable materials for molds and injection molding parts.
- Want quality parts, on time and with fair prices? No one has us beat there.
No middle-man injection molding contract manufacturing.
Each extra step in the supply chain has the potential to decrease communication efficiency and increase costs. We provide you with highly competitive production rates because we work directly with you from our injection molding facilities. - Precision-made tooling to ensure consistency of product.
Pay for tooling once, then never worry about it again. In addition to our tooling optimization processes, our programs include lifetime tooling options enabling you to focus on the product, not the startup costs.
What is plastic injection mold?
Plastic injection molds are designed as hollow metal blocks with cavities used to shape molten plastic through the injection process. There are many holes inside the mold, and the temperature can be controlled by means of oil, water or heater.
Gates in the mold allow molten plastic to flow in, which then fills the cavity through runners and gates. After cooling, the mold is opened, and the ejector pin of the injection molding machine is pushed by the top plate to further eject the molded part.
- Guide Pins– Installed to one half of the plastic injection mold and align the two halves by entering the holes in the other half. the most function is to locate the core and cavity insert in right position, avoid steps on parting line of molding parts or mismatch between two halves of molds.
- Runner– Connect the sprue bush to molding cavities, it is a passageway of flow material, the section shape is usually round or trapezoid.
- Gate–The narrowest position of the runner, where the flow material enters the molding cavity. There are many different types, some will be broken from molding part when ejecting out. such as submarine gate, tunnel gate. Some need to be cut after molding. like tab gate, side gate and so on.
- Sprue (Bush) – Tapered hole in the center of the plastic injection mold into which the flow material travel from the nozzle of injection machine to runners
- Locating Ring– Locating the plastic injection mold on the fixed platen of injection machines, so that the injection nozzle lines up with the sprue bush.
- Mould Cavity(include cavity and core)– The space in the mold shaped to produce molding product.
- The ejector (Pins)– Push the runner and molding parts out of the mold
- The Shot– Total amount of material into cavities, include runner and molding parts
- Ejector plate/Ejector backplate: Just for hold the ejectors in the right position
- Clamping plate: Clamping the mold to the platen of injection machines
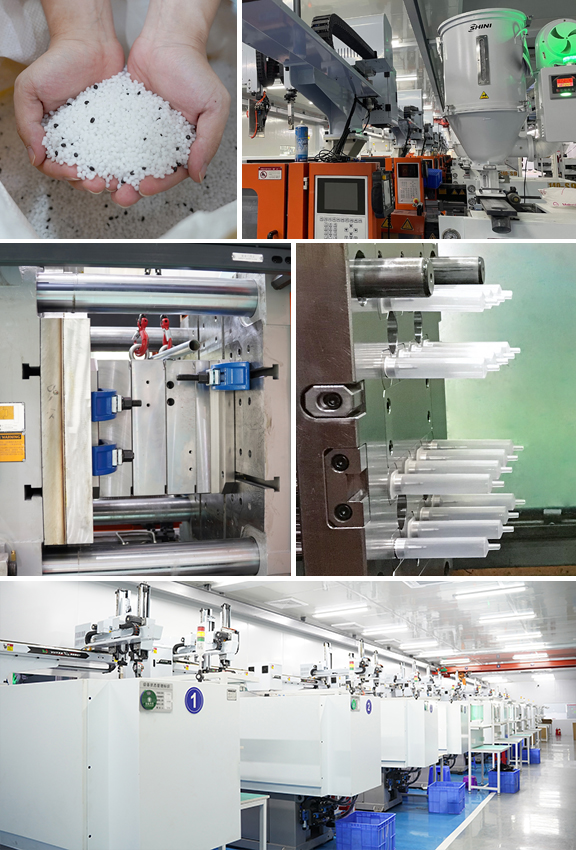
Engineering
We provide a wide range of services to help clients with all of the front-end work that goes into a product before actual production begins. Some of those services include preliminary design, material selection, pricing, mold design, evaluation and procurement, CAD/CAM, surface modeling, and communication with the customer’s engineering department. For each part, we manufacture we will do the DFM study and mold flow analysis which will improve and support the mold structure design.We bring you a combination of the best resources available; high technology equipment, quality workmanship, and program management and product development techniques that are flexible enough to meet the needs of your special requirements that can assist the molder or worker and save time and cost
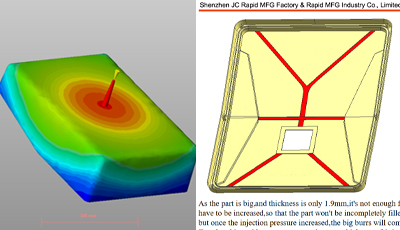
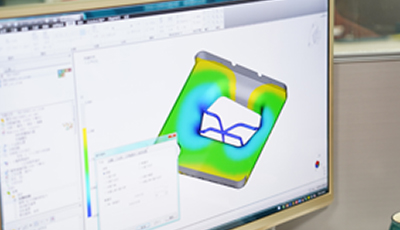
Mold Flow
Quality products and services at the lowest cost and in the quickest time. A universal standard that every company must follow to compete in today’s markets. Every molded plastics part must run smoothly through product design, tool building, tryouts, manufacturing, assembly, field applications, and over the life of products. Our expertise in CAE (computer-aided engineering) in conjunction with the experience of hundreds of molded products provides a valuable link to reach the goal of producing quality products at the lowest cost and in the shortest time. Our engineers will analyze for mold filling, cooling, and warp (deformation) … for every part with the tooling design as well as scientifically validating key steps to make your product a success – designed and built right the very first time. Our unmatched expert approach to every project provides the best value in the long term and will save you cost and time.
Project Management
Project management is the key to the success and quality of the products ,A Project Engineer who has rich knowledge in tooling and plastic injection molding is appointed for each project. All of them have a good command of English.
The project engineers will be responsible to follow up tooling schedule and timely report to the customer on any issues and progress of the project he is handling. The project engineer also guarantees that customer’s technical requirement is followed.
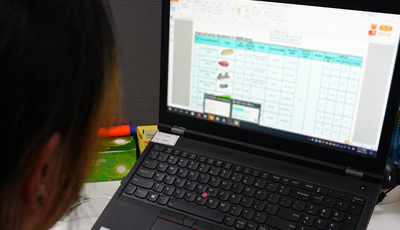
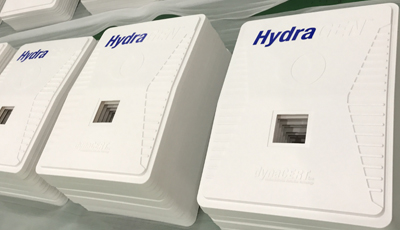
Project Management Objectives
– On-Time Delivery– Assuring customer’s project is produced to customer’s standards and requests
– Anything communicated in a timely and clear way
– Complete project management and support from concept to final part inspection and approval.
Request Your Free Injection Mold Quote Today
Our Most quotes are delivered within 24 hrs, or faster, depending on project details and your injection molding needs. Your customer support partner will contact you directly to ensure you’ve received and understand all aspects of your quotation and to answer any questions you may have about injection molding, the manufacturing process, the materials we use, your quote, and beyond!